The H-Factor – Kerf Bending with Laser Cutting
2021/22 Introduction to Digital Fabrication, Final – Neha Jayanth Pattanshetti, Alessandra Weiss, Luca Wenzel
The H-Factor consisted of an intense exploration and work with different kerf bending patterns. This technique was used to achieve flexibility in the plywood, to allow for the creation of an aggregatable module. The module was assembled with H-shaped press fit joinery that connects the kerf elements to a rounded tetrahedron module. Each module can be connected to another module through the sharing of the H-connector pieces. The aggregation could theoretically continue indefinitely as multiple repetitions of itself.
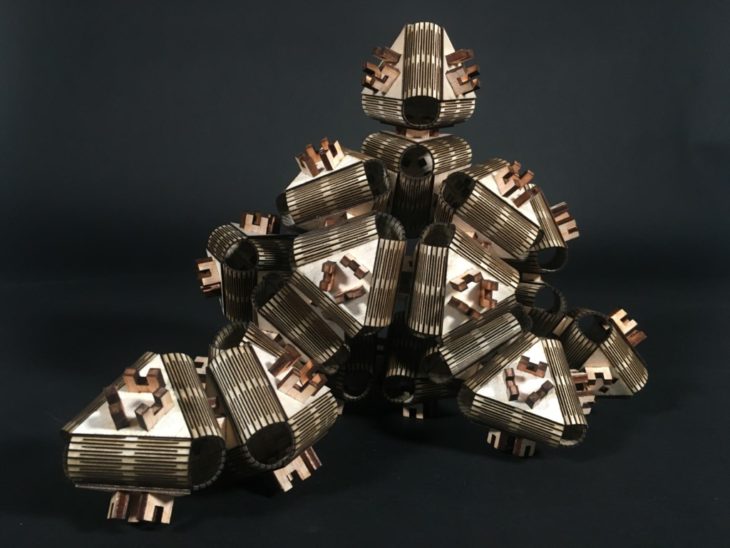
Final Model
Testing
The kerf patterns were tested on 1.2 mm plywood. The tested patterns included: honeycomb cut lines (sparse & dense), wavy cut lines (sparse & dense) and four different iterations of straight-cut lines that differed in spacing and length of each cutting line. Each pattern was tested for good flexibility and bend in one direction and minimal cutting time. Some tested patterns bent the material along a diagonal axis, which produced an undesirable skewing of the module. Most denser patterns did not increase flexibility of the material as assumed, but broke the piece instead. The straight cut pattern proofed to work best and was adjusted in further testing.
The H-shaped press fit joints were cut on 4 mm plywood. Five iterations were made with a variation of 0.1 mm, to achieve a tight fit that was still easy to assemble.
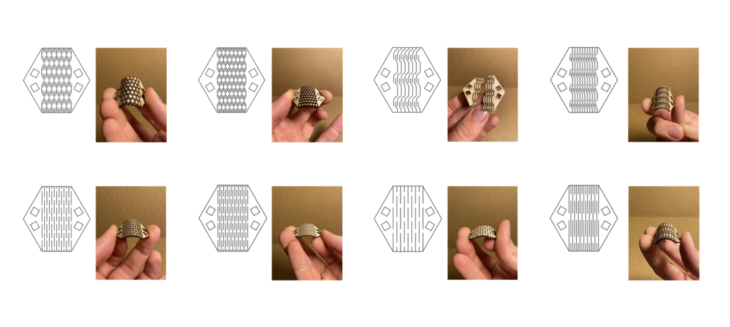
Kerf Pattern Testing
Cutting and Assembly
The kerf elements were flattened to create the laser cutting file. A triangle element was added for extra stability of the connection. Each module was designed to be made of 6 hexagons and 4 triangles, connected by H-joints. The individual pieces were arranged on the plywood sheet with shared outlines, to reduce wastage of material and time.
Every hexagon piece has the kerf pattern in the centre which allows it to bend and join to the next hexagon. 3 hexagon pieces are joined with a triangle. A separate triangle piece of the same size is attached using the H-connections. The module is then completed by bending its individual components to close all connection points. Two modules are then attached together by sharing a single H-connection press fit joint.
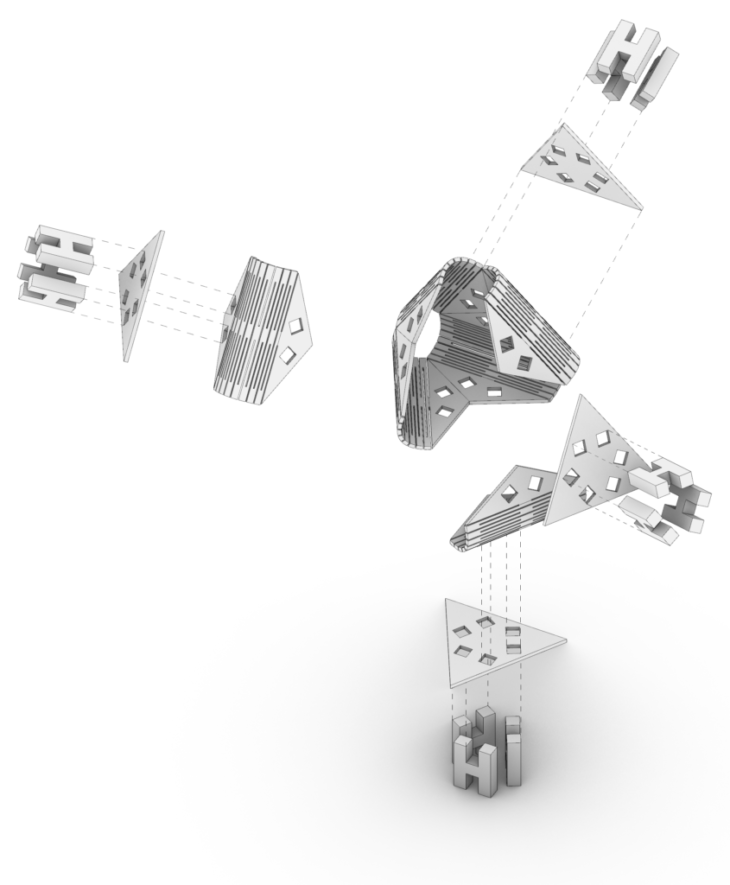
Module Assembly
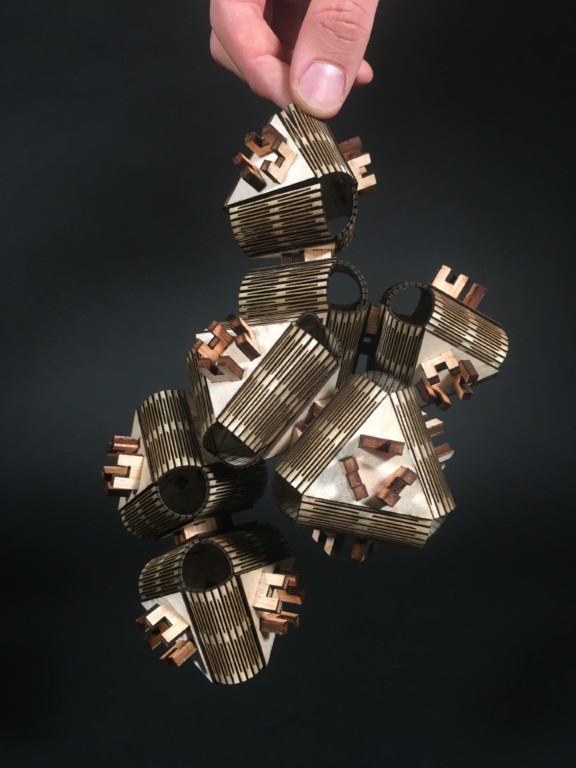
Half Model
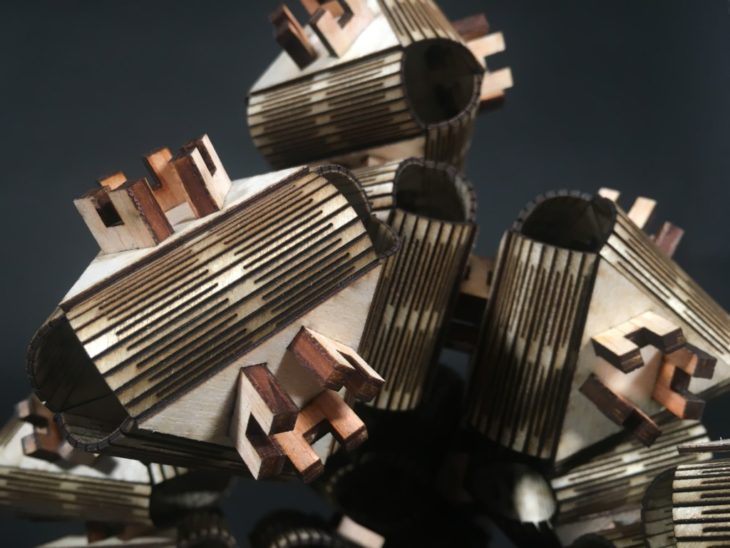
Final Model
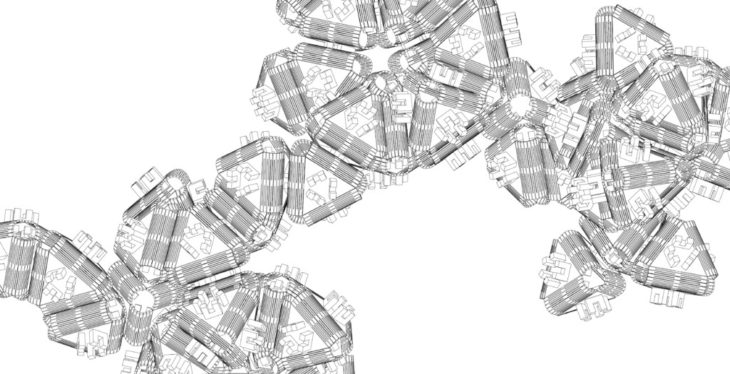
Extended Aggregation
Technical Data
- Machine : Epilog 75 CO² Laser Cutter
- Technique : Laser Cutting
- Joint type: Press Fit Joint
Kerf-Hexagons and Triangles
- Material: 1.2mm birch plywood
- Speed: 35
- Power: 80%
- Frequency: 5000
H-Joinery
- Material: 4 mm poplar plywood
- Speed: 20
- Power: 95%
- Frequency: 300
Credits
The H-Factor is a project of IAAC, the Institute for Advanced Architecture of Catalonia, developed during the Master in Advanced Architecture (MAA01) 2021/22 by students: Neha Jayanth Pattanshetti, Alessandra Weiss, Luca Wenzel; faculty: Ricardo Mayor, Marielena Papandreou