ABSTRACT
The purpose of this project is to create a self-sustainable residential community that does not just solve the technical challenges of becoming the first extraterrestrial species, but thrive on it. The project embraced radical inclusion, decommodification, communal effort, radical self-reliance, participation, and an extreme approach to a leave-no-trace attitude towards our community. The design process was based on modularity, adaptability, self-assembly, individuality, and embracing lunar gravity.
REFERENCES
Few references are studied on both conceptual and technical levels. The first reference is the Archigram plug-in city and how a “megastructure” can incorporate residences, access routes, and essential services for the inhabitants, Plug-in City was designed to encourage change through obsolescence: each building outcrop is removable, and a permanent “crane way” facilitates continual rebuilding. The other references are related to inhabiting the space, LUNARK by Saga architects and the MARTIAN house by Hugh Broughton architects.
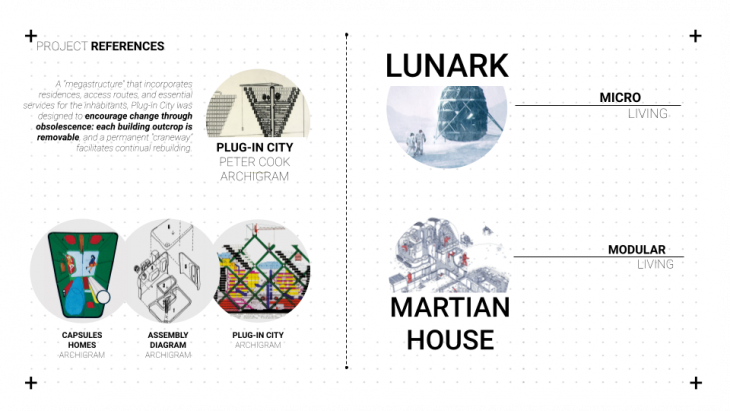
Capsule Homes, Tower and Capsule Elevations, plans and details ARCHIGRAM ARCHIVES AUTHOR: WARREN CHALK 1964. MARTIAN HOUSE ARCHITECTURAL DRAWINGS, HUGH BROUGHTON ARCHITECTS AND PEARCE. ARCHITECTURAL DRAWINGS OF MARK 1 – THE LUNAR HABITAT, SAGA ARCHITECTS.
MATERIALITY
There is a duality of materials that drives the design of our project. This comes from the accessibility to materials on the moon. We need to be resourceful with what we can produce on the moon itself to avoid bringing materials from the earth, and at the same time, we need to address the radiation issue on the moon. Our construction material consists of an additive component, which is the lunar regolith that comes from the moon’s surface. And a hydrogen-filled skin that protects the residents from harmful radiation. Hydrogen acts as a good shield against radiation because of its similar-sized particles.
There are two sources for the raw materials. Ground for the moon regolith and Shackleton crater for water in the form of ice. Choosing this location was essential for the project at the very beginning because of the proximity and availability of our building material. Here you can see the energy requirement for producing the elements we need. Both regolith and ice can produce the hydrogen needed for protection from space radiations.
PARTS CATALOGUE
The whole project consists of seven elements that belong to different categories; residential, structure, and circulation. These units are designed to allow flexibility of the construction and adaptability to connect more units to help the first lunar community grow on the moon. Each part is created by assembling pre-casted components onsite.
There are three residential units to accommodate different families and lifestyle variations. Units are designed to fit two persons, 3 persons, or 4 persons. The communal part is designed to act as a gathering node for social interaction and different activities in between residential clusters.
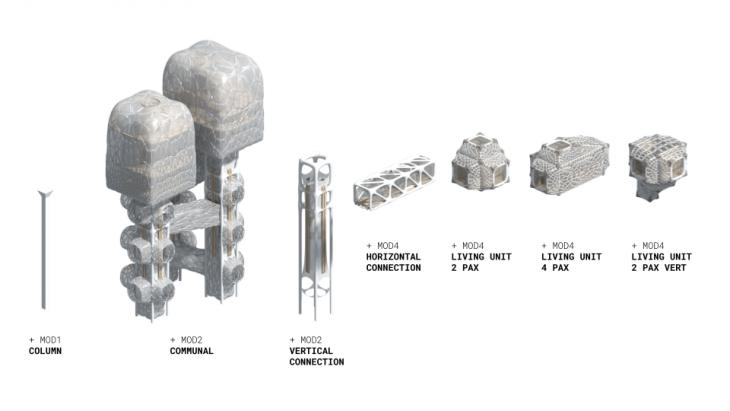
Parts Catalog (Structural columns-Communal spaces-Vertical Connection-Horizontal Connection-Living part A-Living part B-Living part C
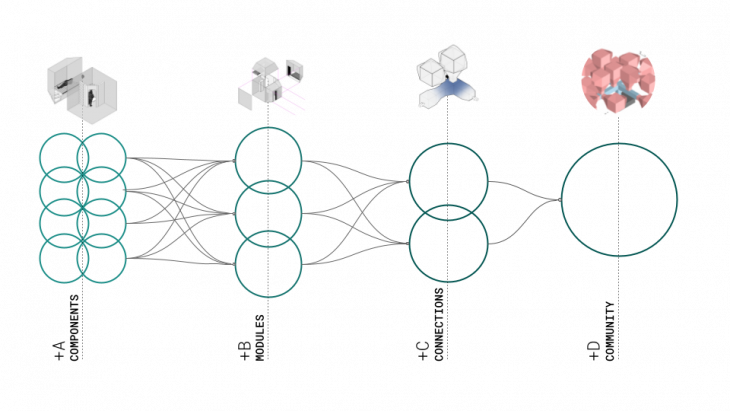
Parts design and connections in different levels of detail.
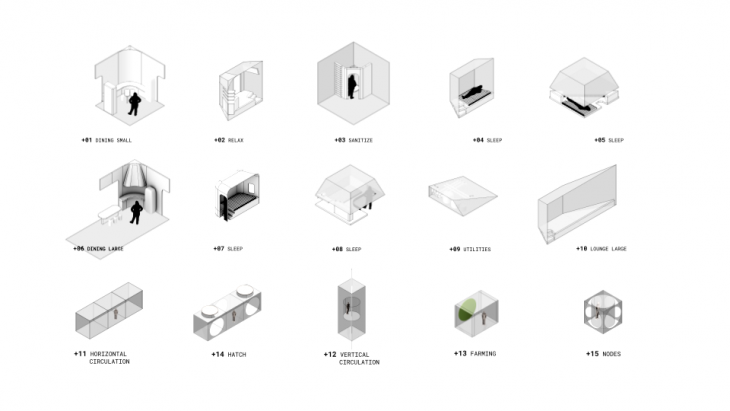
Residential parts pre-casted components.
PARTS MANUFACTURING
The skin of the residential units is designed to protect people inside these units from lunar radiations, so the units are constructed from many layers to create a sort of shelter. Taking into consideration different aspects like privacy, spatial quality, and how we can embrace lunar gravity. The structure consists of 6 different layers:
1- Structural Frame
2- Structural Nodes
3- Weaved Fabric
4- Inflatable Mesh
5- Windows
6- Interior Elements
The units are manufactured by going through the following phases:
1- The 36 structural rod elements are 3d printed, using regolith for thermal-based additive manufacturing with multi-component ceramic materials.
2- The same technology and materials to produce the structural nodes that connect different structural members.
3- Both Humans and robots collaborating together to assemble the structural elements.
4- Assembling of pre-casted interior elements.
5- Different types of robots to be able to weave the fabric mesh around the structural elements that hold the whole structure together and support the inflatable mesh later.
6- A hydrogen robot is connected with an underground tank that collects H2O from Lunar dust and pushes that hydrogen into the inflatable mesh to give it more resistance to the moon radiations.

The GIF shows the manufacturing steps of residential units from Lunar materials
PARTS AGGREGATION
An aggregation system is created to generate modular and adaptable growth. The aggregation is defined by a set of adjacencies rules, growth field, and volume constraint.
The structure starts with setting multiple units and growth vectors toward different neighbors, the seven aggregation parts are connected together later based on the stochastic aggregation rules. These rules are designed to keep the people circulation flow between the vertical circulation, horizontal circulation, and the residential elements.
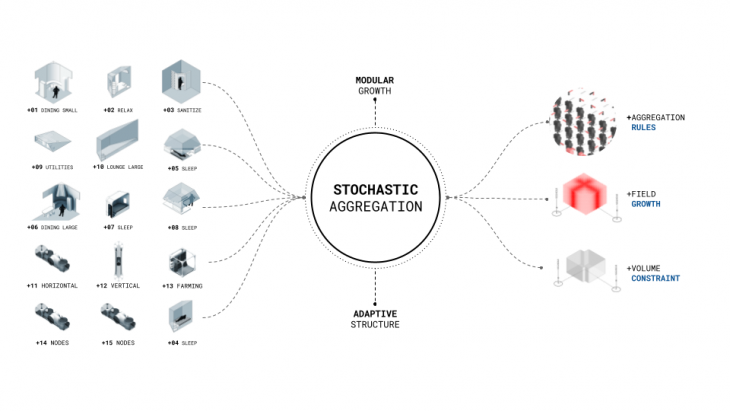
The diagram shows the stochastic aggregation elements.
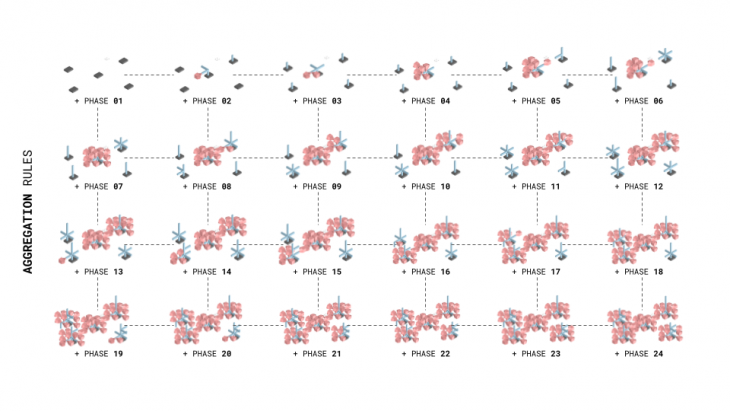
The aggregation growth phases.
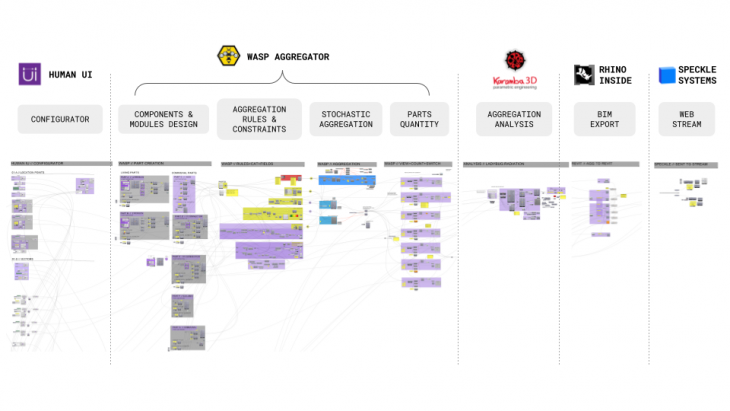
The diagram shows the Grasshopper script and the design workflow.
INTEGRATIVE/COLLABORATIVE WORKFLOW
The following video demonstrating the design workflow that goes through different steps. The workflow designed to keep all of the design parts automated and parametric. The user interface is created using the Human UI plugin to control this complex design process, this configurator has different tabs for each step of the project workflow, going through the aggregation rules, parts quantities, structural analysis, radiation analysis, walkability analysis, Interoperability with Revit and streaming the project on the web.
</p>
INTEROPERABILITY WITH REVIT
A parametric workflow is designed to export geometries from Rhino to Revit using Rhinoinside, six families are first constructed for different parts to create the part itself. The workflow between Grasshopper and Rhinoinside allows the creation of automated drawings such as; sections, plans, axonometric, and exploded models. Revit is also used for quantities and other information automated scheduling to identify how many units, structure elements, and how much materials needed for construction.
COMMUNITY CONSTRUCTION PROCESS
The construction process is created to be flexible and can accommodate the structure’s modularity and adaptability. It can really allow future growth and expansion of this community. The connection nodes between different parts are designed to be flexible enough for future recycling and mobility. And the process should go as the following:
1- start with creating the unit with different structural elements and components assembly.
2- Move these units to different locations using space drones and attaching them to the circulation parts.
3- To use scaffolding elements to construct bigger structures like the circulation parts and communal spaces.
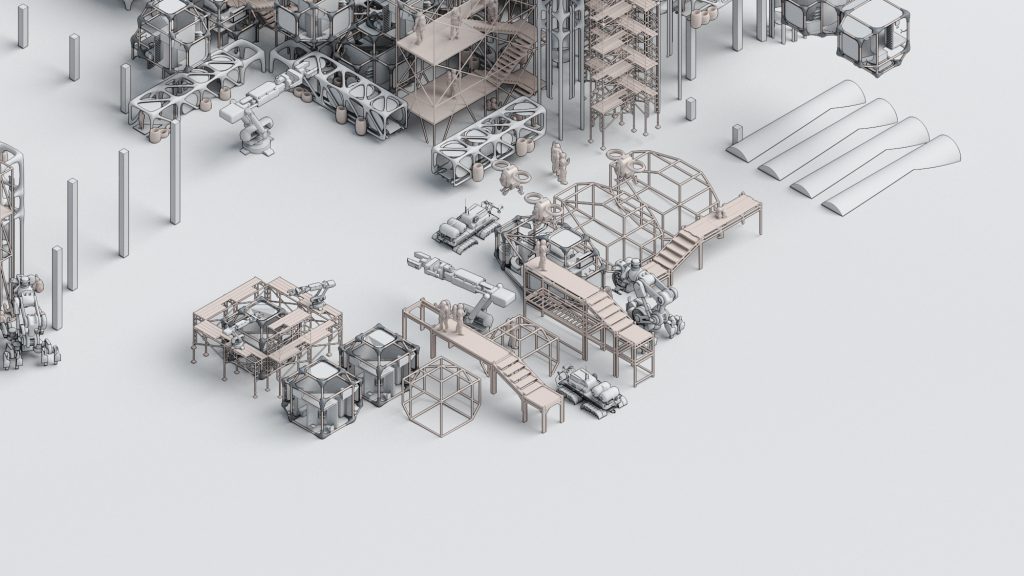
The construction phasing of different units, starting with the skeleton until we get to the final elements assembly.
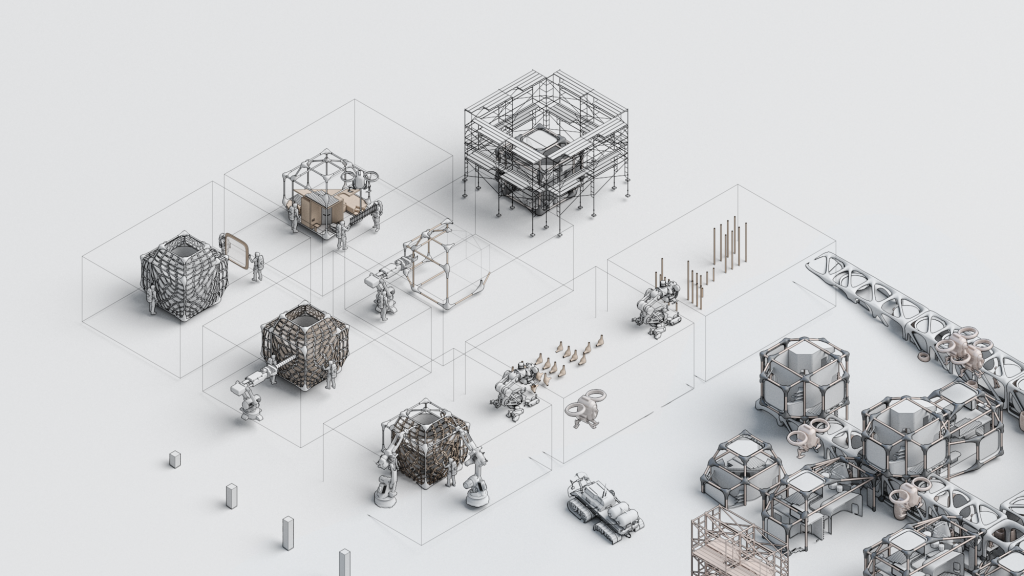
The different unit elements and the machines that are used during that process.

These units carried by space drones to their final destination in relation to the surrounding units and circulation elements.

Using 3D printed scaffolding systems to help to build bigger structures.

A look from inside the circulation parts where people can access their units from it, and it also could be used as a host for green farming systems.

A view from inside one of the units shows the visual connection from inside out and different interior elements.

An elevation view for the community showing the skyline and the project levels.

This is the final configuration of our aggregated community, and here we are creating main circulation paths to other space programs connected with the LNS system, and we can also see how we are creating different voids between residential clusters to enhance the spatial quality and user experience and also to enhance daylighting inside the interiors.
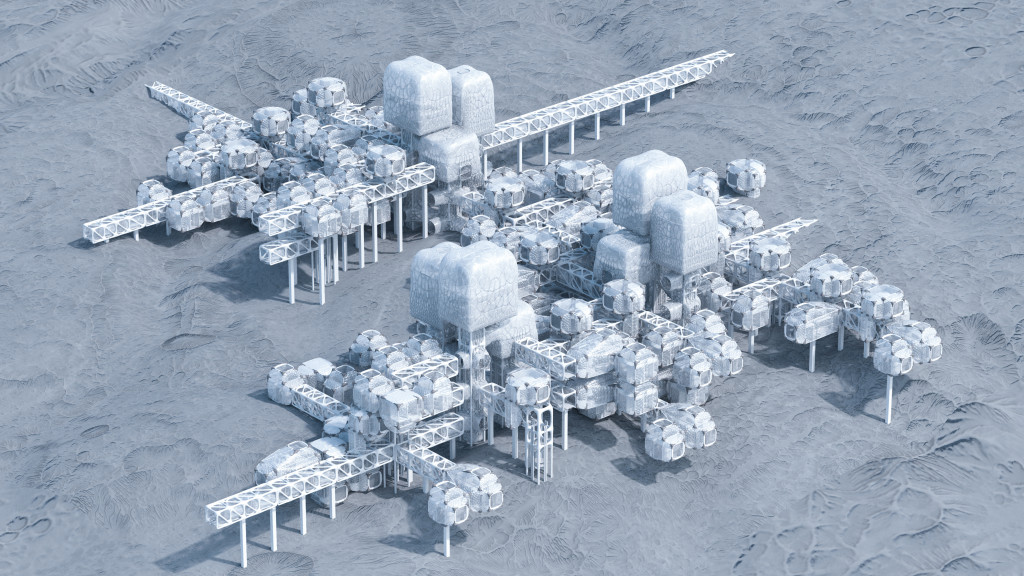
The idea behind having bigger structures in between the units was mainly based on social aspects to improve the wayfinding inside the community, so people can actually identify their units by the visual contact to these landmarks. And also to create a gathering node where people can meet, interact and socialize.

The structure is enabling different levels of visual and physical interaction. And how people are approaching their units by going to the communal space entrance, move vertically and then move inside the horizontal circulation elements and so on.

A perspective showing the spatial organization of the residential units, skin details, and how people are living inside these small residential units. And how we were trying to keep the social interaction between people inside the community to enhance the new way of living on the moon’s surface.
Lunar Residency is a project of IAAC, Institute for Advanced Architecture of Catalonia developed at Master in Advanced Computation for Architecture & Design in 2020/21 by
Students: Marissa Ridzuan + Hesham Shawqy + German Otto Bodenbender
Lead Faculty: David Andres Leon, Faculty Assistant: Oana Taut