Amber Laminaria
Additive Manufacturing of Seaweed as a Biocomposite Material
// MAIN AIM
This research aims to develop and understand additive manufacturing of kelp as a biocomposite material. The use of seaweed as a macroalgae draws attention to current issues of global warming, as it is an underutilized resource and can be used to sequester carbon on a large scale. The research looks at the development of a water-based biocomposite material made from sodium alginate, a derivative from brown seaweed. Through a series of material experiments, a refined bioplastic recipe was determined based on its curing and mechanical properties. This material was then used to 3D print large flat sheets that dried and shrunk into 4 dimensional membranes with unique aesthetic qualities.
// CARBON SEQUESTRATION
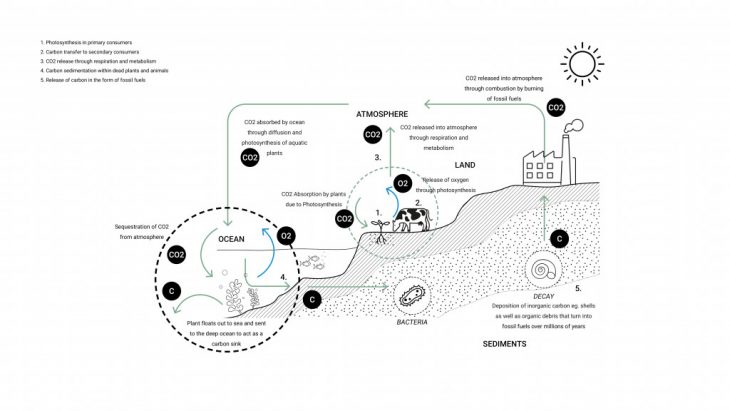
Carbon Cycle
Carbon sequestration is the long-term storage of carbon within plants, soils, geologic formations and the ocean. It occurs both naturally and as a result of anthropogenic activities and typically refers to the storage of carbon that has the immediate potential to become carbon dioxide gas.
Reservoirs that retain carbon and keep it from entering the Earth’s atmosphere are known as carbon sinks. The amount of carbon stored in the oceanic sink exceeds the amount in the atmosphere. In response to growing concerns about climate change, considerable interest has been drawn to the possibility of increasing the rate of carbon sequestration through natural technologies within the ocean.
The oceans itself accumulates carbon within coastal ecosystems, known as Blue Carbon. Blue Carbon coastal ecosystems occur in shallow waters and account for 48% of long-term carbon sequestration and only make up 2% of the ocean. Blue carbon ecosystems such as seagrass meadows, mangrove forests and salt marshes store away most of this carbon.
Another overlooked biomass that can be utilized is seaweed. Seaweed fragments that float out into the open ocean are a mechanism to permanently store blue carbon at depth or on the seafloor. New studies are currently documenting the potential of seaweed farming to counter climate change as deforestation decimates rainforests and other crucial carbon sinks. Fast-growing sea jungles of kelp and other macroalgae are highly efficient at storing carbon. If we were to farm seaweed in a sustainable way, it could mitigate climate change, promote marine biodiversity and promote jobs in local communities.
// SEAWEED AS A SPECIES
Seaweed is a macroalgae that grows in a variety of forms and colours in the ocean as well as freshwater environments. Seaweeds are currently used in a range of products within the food, medicinal and cosmetics industries. It is also used as a natural fertilizer and adding seaweed to livestock feed can reduce the methane emissions from cattle.
Seaweed is a term that can be used to describe many different marine-based species of plants and algae. There are likely to be thousands of species of seaweed. It can be broken down into 3 main categories by the colour, which is a direct result of the amount of sunlight absorbed and how close it is to the ocean’s surface. Brown seaweeds such as giant kelp are the largest of all marine algae and can grow up to 30m in length. Kelp forests thrive in cold, nutrient-rich waters and rely on sunlight to generate food and energy. Kelp forests do not overlap with other coastal ecosystems previously mentioned as they grow in more tropical climates.
Seaweed is a relatively new and unexplored material within architecture and design. These projects incorporated a range of different types and applications of seaweed and eelgrass. It can be seen used in it’s raw form, combined and cooked to create a biocomposite, moldable material, or used as a traditional material to insulate buildings. Other more recent investigations are going into seaweed as a bioplastic or textile.
A first set of experiments were conducted by drying large pieces of kelp in various ways in order to understand the material and its characteristics. However, I felt that kelp in its raw form was limited in terms of scaling up and so I looked to other extraction of its form. Sodium Alginate is an extraction of brown seaweed.
// BIOCOMPOSITE MATERIAL SYSTEM
Sodium Alginate is a biopolymer extracted from the cell walls of kelp. It is a natural hydrophilic polysaccharide which is non-toxic, biodegradable and antibacterial and used in food and biochemical engineering. It is a thickener and gelling agent seen in products such as ice cream and toothpaste. Sodium Alginate can cross-link with calcium ions creating alginate gels. This cross-linking of ions was used as a way to make the material water resistant later on in the research project.
Sodium Alginate and other seaweed based biopolymers such as agar and carrageenan are used in the making of bioplastics. Bio-based plastics are made wholly or partially from renewable biological resources, and are composed of biopolymers for strength, plasticizers for flexibility and additives for other qualities.
A cooking process is used to make bioplastics where measured powders are added to a certain amount of water and heated to a certain temperature until everything has dissolved into a homogeneous mixture. A plasticizer is then added and the mixture is poured into a frame and set to dry at a low temperature in an oven for a few hours. This is the basis of making bioplastics. This recipe was used and altered to make the first set of experiments including sodium alginate as the main ingredient.
https://materiom.org/
A set of experiments were conducted with slight changes of amounts of materials were added in order to get an accurate representation of the characteristics and qualities that each material gave. Fibers were also added to see how the material would change as it shrunk and deformed.
Based on these sets of methodical experiments, certain aspects of the material were extrapolated. The way in which the material dried and shrunk through the process of evaporation was a key aspect that could be explored further. The material is of a thick consistency when wet, which was perfect for 3D printing.
A recipe was chosen based on the outcome of strength, translucency and flexibility of the material. This base recipe was then used and built upon for the rest of the research. The addition of another biopolymer, cellulose powder, which is the most abundant biopolymer in the world, was added in order to improve the characteristics of the material in which sodium alginate is lacking such as poor water vapor barrier and mechanical strength.
// ADDITIVE MANUFACTURING OF THE MATERIAL
The manufacturing of bioplastics on a large architectural scale is also relatively new. I looked at some references of robotic fabrication of water-based biocomposite materials and how these designers designed with materials that are susceptible to shrinkage. Additive manufacturing strategies were explored in order to produce larger products with precision and control.
Casting, as seen in the initial experiments, was limited in size, therefore 3D printing was explored. The material had the potential to print 3 dimensionally, however the results (because of shrinkage due to high water content) were not desirable. Sheet printing was then chosen instead.
3D printing is affected by different parameters which affect the outcome of the prints. Unlike most other materials in 3D printing, this kelp biocomposite is strongly affected by the directionality of the machine’s toolpath. Small tests were done in order to understand this. The material shrinks and pulls in the direction in which it was printed. Nozzle shapes and sizes were briefly explored when looking at spreading the material as quickly as possible.
These tests were translated onto a bigger scale using the ABB140 robot where sheets of up to 1m in length could be printed. Flat, one layered sheets with different toolpaths were printed successfully creating flexible and translucent membranes that were working well in tension but not well in compression.
By combining a shape outline or border with a regular toolpath pattern, an evenly distributed sheet could be printed. This was to prevent the material from spreading outside of the desired shape. This sheet would shrink in height and length and curl upwards away from the flat acrylic surface.
Adding a second layer on top of the flat sheet was a turning point in the research as this gave the sheets certain unique characteristics that had not been seen before. The layered sheet would take between 7 and 10 days to dry (depending on the size of the sheet). Over the drying period, the surrounding conditions were crucial in the outcome of the prints. The room temperature and humidity were important factors to consider during this process.
The first of the two layers was printed as seen previously, with a border and infill running along the width of the shape. The top layers, however, were designed to act as a substructure made from the same material. Due to the placement of these ribs vertically and horizontally, an equal distribution of shrinkage occurred throughout the sheet. The most interesting outcome was the sine wave created on the edge of these sheets due to these ribs.
A catalogue of shapes and strategies were tested all with 2 to 4 layers and a combination of 4, 6 and 8 mm round nozzles. All sheets were recorded and analyzed on their size, percentage of shrinkage, as well as effects of translucency, strength and flexibility. It can be seen that the sheets shrink 10 to 20% in length and 5 to 10% in width.
// SELF-HOLDING MEMBRANE
Distinct characteristics emerged, showing that as much as one tries to control the material, it has a mind of its own. Ribs emerged on the underside of the sheets, uniform sine waves appeared along the edges, beautiful translucent patterns were seen with light, and gaps and openings started to emerge during the shrinking process where there was not enough overlapping material or weak points in the print.
An exploration into natural structures that could hold themselves was done. It was seen that veins within leaves and dragonfly wings were light but strong and flexible. These were driving factors into the development of the shape and structure of the printed sheets. As they dried they would form self-holding mono-material structures.
The idea of the self holding membrane would be that the material would not require a substructure as it would be able to act as a membrane as well as its supporting structure. However, once a Karamba analysis was done, a weak point was found, which would cause the material to bend. This could then be avoided by adding a minimal substructure using bent timber / glulam created to the desired curve.
// SCALING UP
Now that there was an understanding and certain depth of control of the material, we could scale it up and create a 2m long sheet using the Kuka robot. This was printed over the period of one week. The first layer was printed on Monday and took 10 days to completely dry, with many unforeseen outcomes.
// ARCHITECTURAL APPLICATION
By creating, fabricating and designing using a biodegradable, biocomposite material, one is able to design an architectural strategy that would not contribute to carbon emissions but sequester them through the encouragement of seaweed production. A circular design can be created in order to bioremediate soils in the surrounding area while using local materials that have been sustainably grown.
Some prints were printed for the timber rooftop which is located on top of IAAC’s rooftop. The panels could be both looked at as shading elements and aesthetic accessories on this structure. The membranes seem to come to life when exposed to natural sunlight, illuminating them.
</p>
Amber Laminaria: Additive Manufacturing of Seaweed as a Biocomposite Material is a project of IAAC, Institute for Advanced Architecture of Catalonia developed in the MAA02 2019/2021 by: Student: Ilaena Mariam Napier and Faculty: Marcos Cruz and Kunaljit Chadha