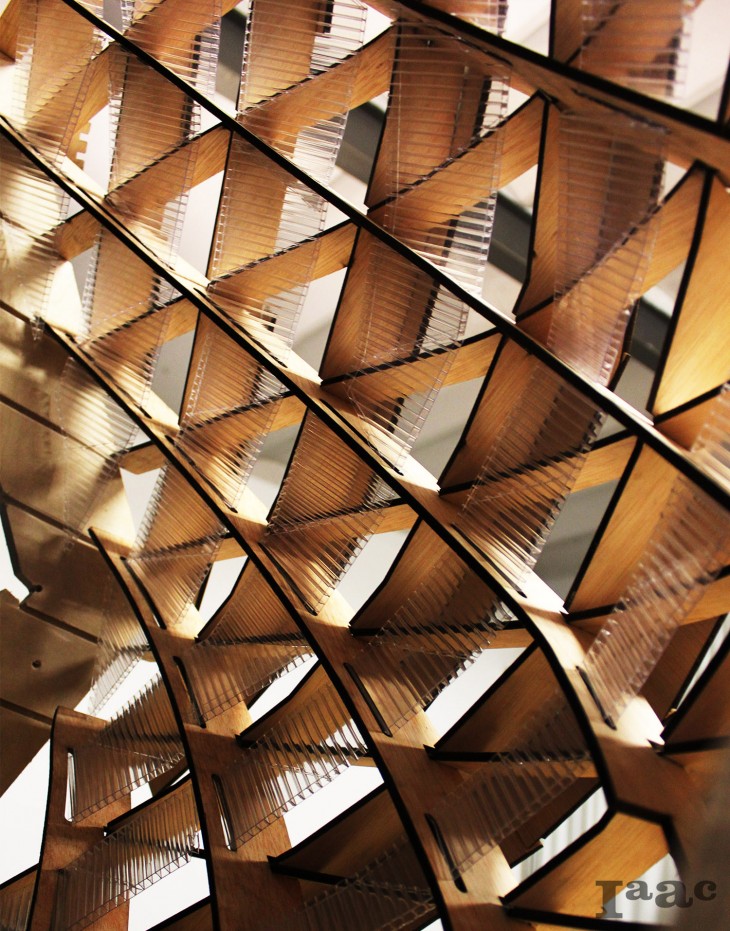
Tri-Axial ‘waffle’ structure
CONCEPT
Our facade module aims to optimise the internal light and air quality for the proposed Wiki-House. The facade is supported on 5 mm plywood tri-axial ‘waffle’ structure. The structural struts are notched and easily accommodate curves in the x,y and z axis, good connections at each tri-axis provide the strength in the system. Therefore, this system requires the minimum amount of material.
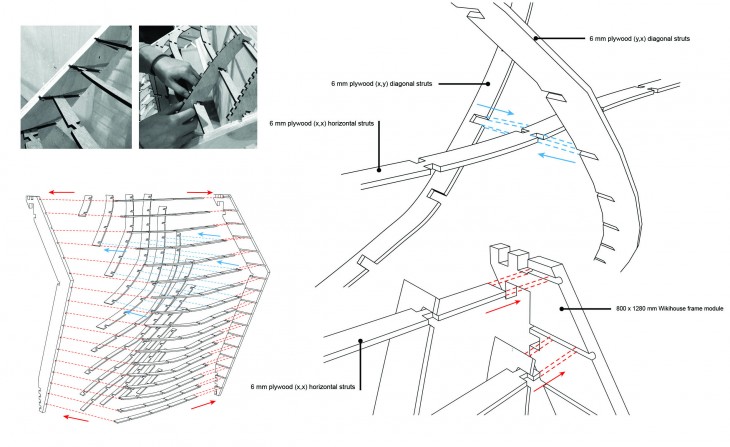
Diagram Detail
6 mm translucent polycarbonate sheeting is incorporated as an element in the axis of the structure permitting the entry of sunlight, while protecting from harmful uv rays and shielding from the rain. The hollow-core composition of the polycarbonate sheeting will provide insulating qualities to the facade. The waffle systems shallow depth provides a louvred effect to the building, excessive direct sunlight is mitigated by flat elements jointed to extrusions on the profiled structure. The shading elements are varied according to there orientation to the south-west placement on a site in Barcelona. The hollow-core composition of the polycarbonate sheeting set against the plywood will provide insulating qualities to the facade. The completed pre-fabricated module shall slot into the skeletal frame of the laboratory, without requiring mechanical fixings.reducing the need for mechanical forms of climate control.
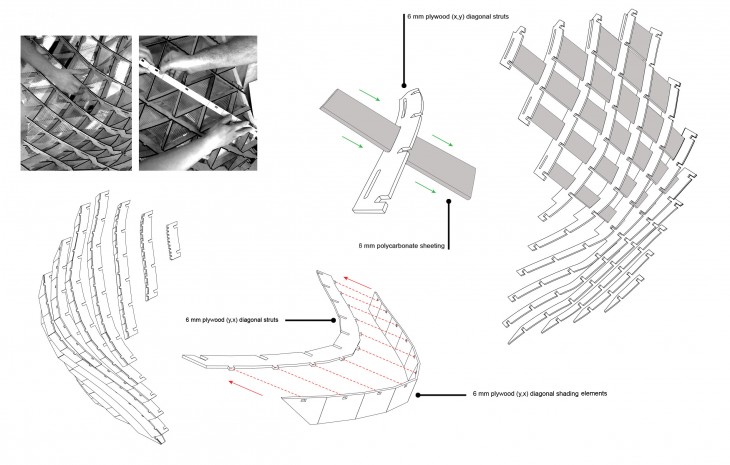
Diagram Components
METHODS
A number of steps were undertaken to obtain the final structure. We incorporated various methods of design in both analogue hand drawings and digital tools with rhinoceros3d and grasshopper3d. Considerations undertaken in the final design of the material limits/behaviour of our designated material composition of 80% wood and 20% polycarbonate. We understood the material properties of wood to be able to flex to a certain degree as well as the limitation of the direction properties of polycarbonate. Although this was the case, we did experimentation on the possibility to change or tweak the behaviour to a certain degree. Several 1:1 tests were made to observe the tolerance needed for 3 axes to interlock neatly. Testing of the components were also conducted to ensure suitable tolerances as well as potential joining methods to the structure. Once we were confident with all the data from our experiments, we fabricated the wooden slices in the laser cutter. The profiles were extracted from the 3d Digital model and laid out in the specific wooden sheets.
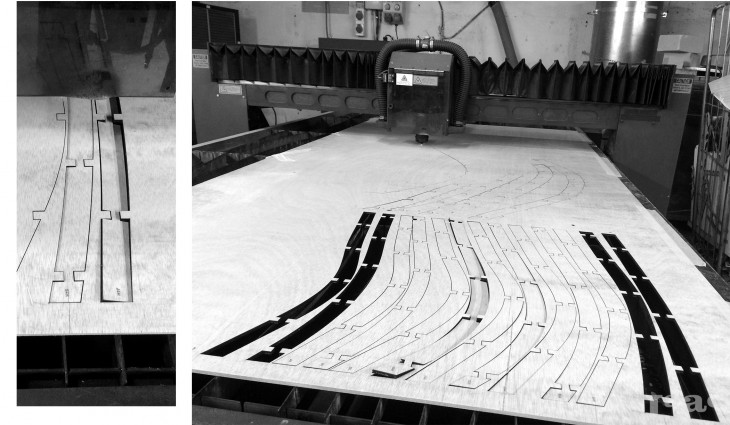
Process
Polycarbonate strips were cut from the large sheets along a specific direction, to also make use of the material’s internal profile. The containment frame of facade were also modified in order for our structure to slide into. Channels of the same thickness of our horizontal slices were milled into the given structure, which accommodated the “fixing” of our facade to the frame.
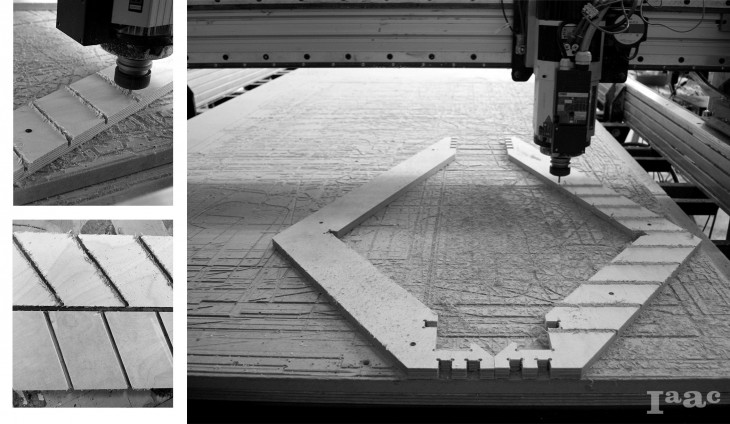
Process
The method of constructing the final structure then, was to assemble the fabricated pieces in a particular order. First, we inserted the horizontal pieces into the frame as the rigid elements and accurate spacing of entire facade. Once this was completed, we overlayed the pieces that locked the structure in one diagonal direction to obtain even more rigidity. The last step was to insert the diagonal slices from the back.
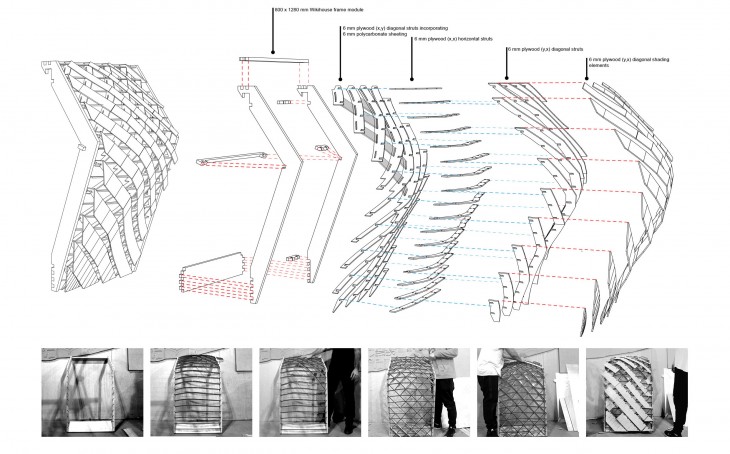
Diagram Facade
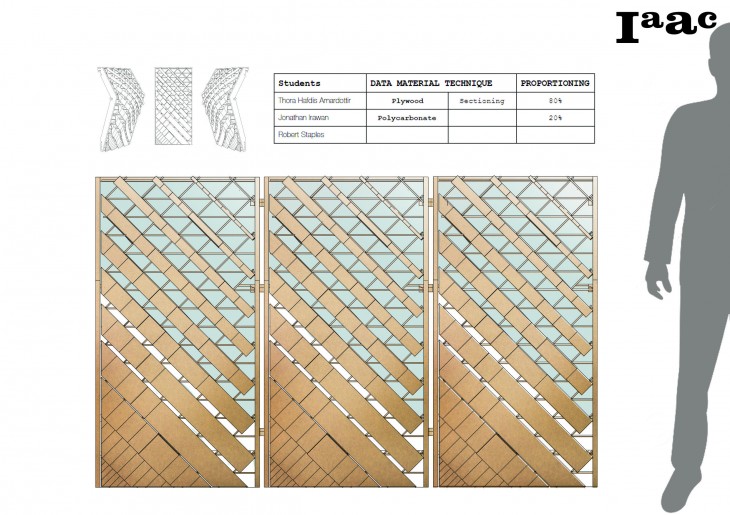
Facade
IAAC, Digital Fabrication.
The tri-axial ‘waffle’ facade is a project of IaaC, Institute for Advanced Architecture of Catalonia developed at Master in Advanced Architecture, MAA02 in 2015 by:
Students:
- Thora H Arnardottir
- Jonathan Irawan
- Robert Staples
Faculty:
- Alexandre Dubor
- Djordje Stanojevic
- Ricardo Valbuena
- Martin Seymour