ABSTRACT }{
For the digital tools for Complex Forming seminar we’ve created a pavilion inspired by the math of pasta. Through the support of McNeel community created a python script to generate an aggnioli pasta shape. We have identified the most form impacting values and connected them to a structural optimization process in Karamba for grasshopper based on the minimum displacements of the structure. An evolutionary solver – Galapagos for grasshopper, was used to populate generations of pasta. The final shell was informed by a live physics simulation using Kangaroo (in grasshopper).
Team: Maria Papadimitraki + Clemens Russ
DESIGN CONCEPT }{
The aim of the project was to create a pavilion inspired by the math behind pasta. As it is placed in the Viennese Prater, it should provide a shelter against strong winds and create a climbing structure for children.
NATURAL SYSTEM }{
“In nature, materials are expensive and shape is cheap as opposed to technology, where the opposite seems to be the case” Julian Vincent.
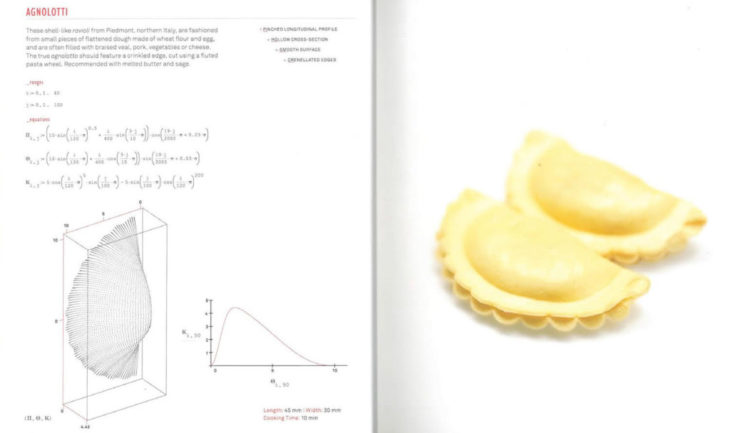
“Pasta by Design by George L. Legendre, 2011”
The strength of the sea shells is naturally informed by sine + cosine functions, that are swept along each other. Some seashells develop kinks alongside the shell surface which are decreasing the bending moments of the shape.
LOCATION }{
Prater park, Vienna, Austria
”Wurstlprater”: funfair (former Expo area)
Prater”: urban forest, playgrounds, rewilded area “Prater-Auen”
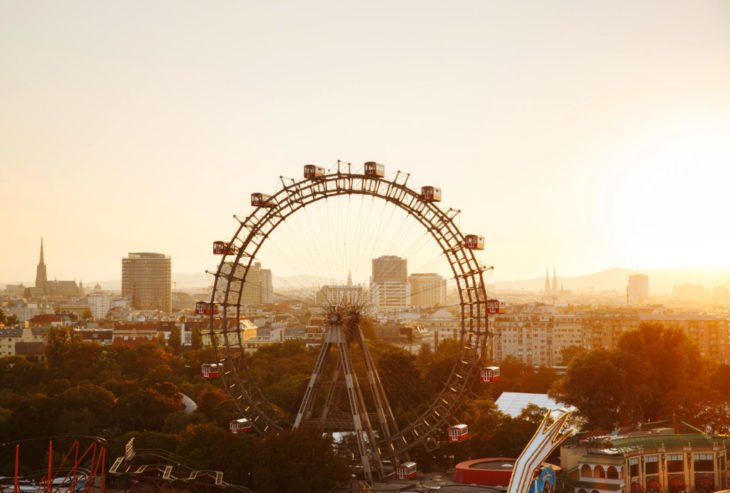
Prater Park, Vienna, Copyright: www.wien.info/en/sightseeing/prater
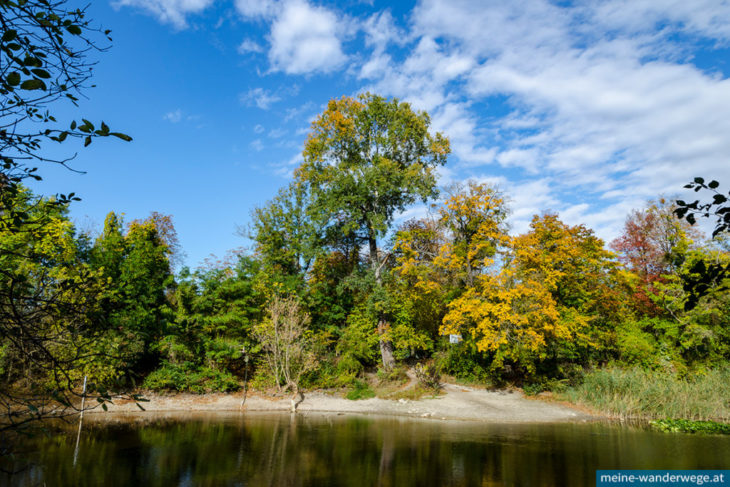
Prater-Auen: Lusthauswasser – Mauthnerwasser, Copyright: meine-wanderwege.at
COMPUTATIONAL DEVELOPMENT }{
- script based on python + rhinoscript
informed by the book: “Pasta by Design by George L. Legendre, 2011”
discourse, McNeel community - structural shell analysis in karamba for grasshopper combined with evolutionary solver galapagos for population + topological optimization (in grasshopper)
- live physics simulation for the final shell using kangaroo (in grasshopper)
DESIGN PROCESS }{
By trying out the python script we’ve created some manual iterations of the shape. furthermore we got appetite for destruction by generating pasta through an evolutionary solver.
2 x 900 generations,
solver: max stagnant: 50, population: 20, maintain: 10%, inbreed: 75 %
thickness: first 15 cm, then 5 cm
material: wood, CLT
span: 20 x 7 x H 5 m
fitness value: reduce displacement of the shell to a minimum
genomes: kinks in Y, Z, X, kink amount + height of the overall structure
loads: 1) gravity, 2) mesh-load 1,5 kN in Z on generated mesh, therefore structure behaves like a catenary structure
OPTIMIZATION PROCESS }{
a la carte: from our set of generations we’ve picked one of our champions and investigated further on it.
Topological shell optimization using galapagos + karamba
2132 generations / 57000 generations
solver: max stagnant: 50, population: 20, maintain: 5%, inbreed: 75 %
thickness: first 15 cm, then 5 cm
material: wood, CLT
span: 20 x 7 x H 5 m
fitness value: reduce displacement of the shell to a minimum
genomes: kinks in Y, Z, X, kink amount + height of the overall structure
loads:1) gravity, 2) mesh-load 1,5 kN in Z on generated mesh, therefore structure behaves like a catenary structure
conclusions – structural analysis and optimization:
the optimization process showcases very promising results.
15 cm thickness:
the optimization dropped the utilization rate to 8.6 % of the structure, the displacement value went down from 3 cm to about 2mm based on 2 iterations, we were able to decrease the thickness of the ?tness value to 5 cm and furthermore to 1,5 cm.
1,5 cm thickness:
displacement values are still low given the 20 m x 7 m span of the pavilion. max. displacement = 2.88 cm
3 cm material was chosen in order to guarantee a sustaining system.
utilization raised to 79.6 %. as the force?ow graph shows, the load is well distributed, therefore 80 % is a desirable + well balanced value.
sustainability:
?rst iteration of the optimization process enabled us to decrease the material thickness from 15 to 5 cm.
this decreases the overall weight of the structure by 466 % from 14 t. to 3 t.
second iteration enabled us to decrease the thickness to 1,5 cm, i.e.: plywood
STATE OF THE ART + PRECEDENTS }{
Thallus Installation – Zaha Hadid Architects
location: Milan, Italy Pinacotera di Brera
event: Milan Design Week
year: 2017
dimensions: 2.01 W x 2.07 D x 2.88 H
material: Premium Polyactide Plastic (PLA) Formfutura Frosty White using robotic additive manufacture
fabrication: Six-axis robotic 3D printing technology 7km extruded structural strip as a continuous line
SHELL DESIGN }{
Running a live physics simulation using kangaroo for grasshopper, we were able to emulate a spaghetti shaped lattice on our base surface. Due to aesthetic reasons we decided against planarized panellization strategy in order to create a more form and topic related outer surface. Therefore we used 4-5 types of our generated pasta shapes and ran the simulation on it. For the simulation we used different types of curves and lengths, which we mapped on our surface. Later on we released them, in order to enable the differential growth alongside the surface, whilst avoiding collisions we used the following “goals” in kangaroo:
- collider
- length
- angle
MANUFACTURING APPROACH }{
For the manufacturing process we went in two directions: a multi-layered offset to generate an overlapping, but not intersecting 3d printing lattice. It can be easily tiled depending on the printer size. The density of the lattice can be increased by adding denser curves or further layers to the structure.
- 5 layers
- 20 mm per layer
- pipe diameter = 20 mm
We also tried a single layered approach, that creates an entire surface from one released curve on the surface
THE BEAUTY OF PASTA }{
THANK YOU!
THE POWER OF PASTA is a project of IAAC, Institute for Advanced Architecture of Catalonia developed at Master in Advanced Computation for Architecture and Design (MaCAD) in 2021-2022 by students Maria Papadimitraki and Clemens Russ and faculty Rodrigo Aguirre and Hesham Shawqy.