Structural Design in the Era of Computational Design and New Age Fabrication Technologies
Computational design and fabrication are at the focus of advanced practice and research in architecture.
-Jan Knippers (University of Stuttgart)
Credits: Caitlin Mueller
When we talk about structures fabrication is an important aspect to consider. All this while the tools provided us the ability to build structures, with the advancements in tools and methodologies advancement in complex structure design also happened. The divide between Architectural Design and Structural Engineering has existed for many decades now, they are two sides of a same coin the coin being the buildings. These barriers between Geometric design and Performance Analysis, Craft and Materialization and Mechanical Properties, Conceptual thinking and Analytical Thinking crystallizes and it becomes hard to be productive in this environment. An integrated way to collaborate would be through Computation, Fabrication and Education.
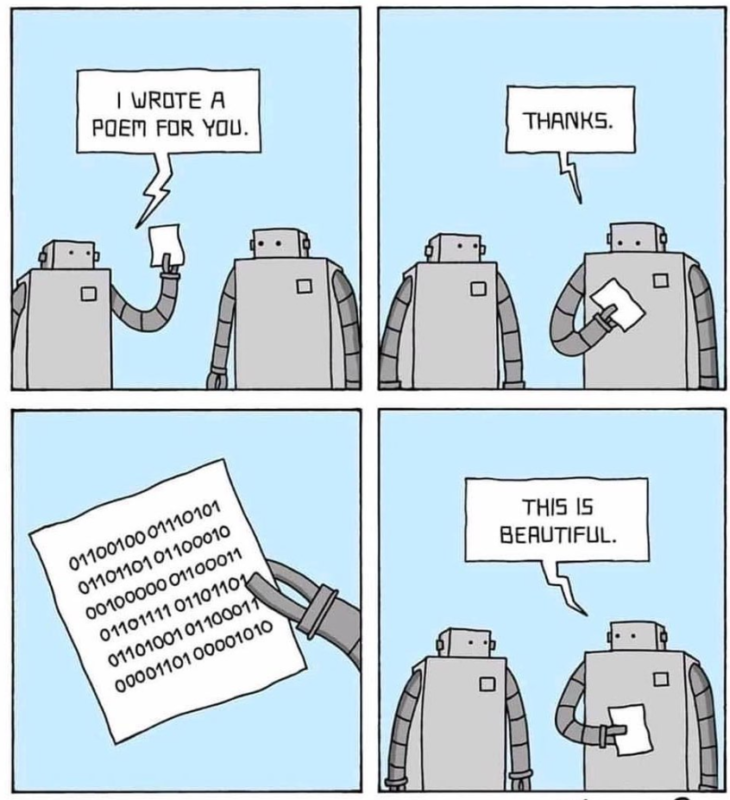
Computer communication through 0 and 1
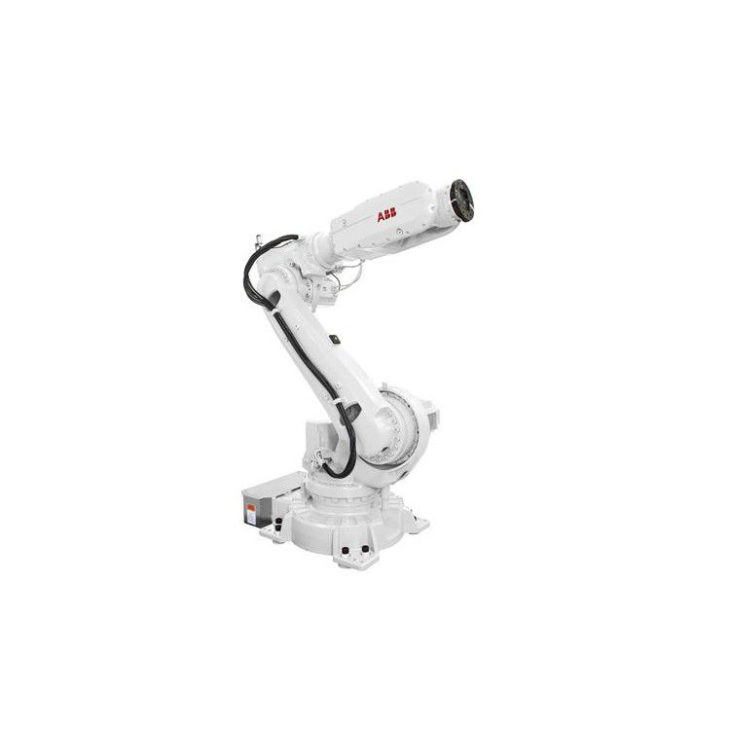
Robotic Arm
Credits: ABB Group
PROJECT-1 The 2014-15 Research Pavilion (Achim Menges)
The research pavilion was built by the Institute for Computational Design (ICD) and the Institute of Building structures and Structural Design (ITKE) at the University of Stuttgart led by Achim Menges. The pavilion demonstrates the architecture potential of novel building methods inspired by the underwater nest construction of the water spider. This pavilion is fabricated using a process in which an industrial robot is placed within an air supported membrane envelope made of ETFE. This inflated soft shell is initially supported by air-pressure, though by robotically reinforcing the carbon-fibre, it is gradually stiffened into a self-supporting monocoque structure. The carbon fibres are only selectively applied where they are required for structural reinforcement, and the pneumatic formwork is simultaneously used as a functional integrated building skin. This results in a resource-efficient construction process.
Source:
Source:
Source:
PROJECT-2 Stress Line Additive Manufacturing (SLAM) for 2.5D Shells (Caitlin Mueller)
The research on SLAM technique was conducted in 2016 by Caitlin.T.Mueller and Kam Ming Mark Tam. The research states that with advancement in the Additive Manufacturing (AM) has enabled fabricating complex geometries easier but AM produces anisotropic materials whose strength varies in the direction of the filament orientation thereby limiting its application. This research developed on the common design platform such as Rhino, grasshopper and Karamba that calculates principal stress lines and Force Flow Lines on a form found 2.5D membrane structures. It was found that a discretized shell structure with a grid base was 20% less structurally efficient than a stress line based topology.
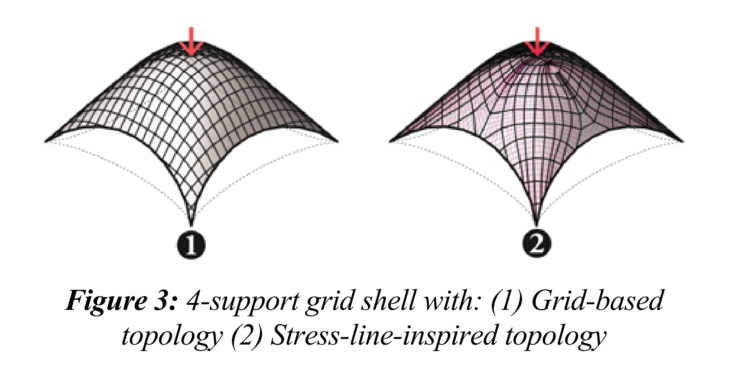
Source :
https://www.researchgate.net/publication/310644805_Stress_Line_Additive_Manufacturing_SLAM_for_25-D_shells
The research reconsidered the traditional AM technique of fused deposition Modelling (FDM) by adding material explicitly along the principal stress trajectories. A 6-axis industrial Kuka robotic arm and a heated extruder was used and provides an alternative to traditional layered manufacturing by allowing for oriented material deposition.
Source :
https://www.researchgate.net/publication/310644805_Stress_Line_Additive_Manufacturing_SLAM_for_25-D_shells
PROJECT-3 Mobile Robotics Fabrication system for Filament Structures (Maria Yablonina)
The project is developed at Institute of Computational Design (ICD) and the Institute of Building Structural Design (ITKE) at the University of Stuttgart suggests a new way of building with fiber composites.
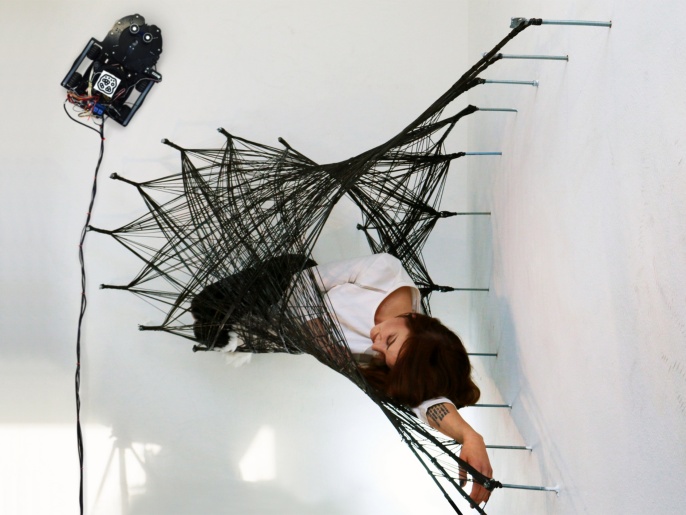
Credits: Maria Yablonina
https://www.mariayablonina.com/mobile-robotic-fabrication-system
https://www.mariayablonina.com/mobile-robotic-fabrication-system
This decade robotic fabrication in the field of architecture has developed rapidly. The project focuses on new generation of mobile construction robots capable of operating on site as compared to the standard industrial machines, originally designed for assembly line applications, which have scale and process limitations.
https://www.mariayablonina.com/mobile-robotic-fabrication-system
https://www.mariayablonina.com/mobile-robotic-fabrication-system
https://www.mariayablonina.com/mobile-robotic-fabrication-system
The research proposes multiple robot cooperative system in the context of surface, facade and wall climbers. The project research focused on developing a locomotion system for constructing complex three-dimensional structures. Architectural walls and ceilings are used as an anchoring surface allowing the robots to operate under the complex unstructured environment. The project has been developed on both hardware and software level to make the interaction between the mobile robots seamless. In the particular scenario of wall climbing, the robots use vacuum motor to carry additional 10 Kg to its own weight. Four independently controlled actuated wheels allow for the robot to accelerate, steer and rotate in place. Visual sensors (cameras) has been mounted o the bodies of robots allowing to system to capture the whole fabrication process and send data back to the machines as a constant feedback. At every iteration before a control signal is sent to the motors, the current acceleration vectors are compared to the desired one in order to calculate a trajectory correction. For global variations path finding algorithm is employed. Once the fabrication process begins, all the robots movement are choreographed autonomously. The vacuum motors used has a high power demand, which makes it necessary to supply power via cable.
https://www.mariayablonina.com/mobile-robotic-fabrication-system
Structural Design in the Era of Computational Design and New Age Fabrication Technologies is a project of IAAC, Institute for Advanced Architecture of Catalonia developed at Master in Advanced Computation for Architecture and Design (MaCAD) in 2021/22 by student Naitik Sharma and faculty Jane Burry.