ROBOTIC AND MIXED REALITY
WORKSHOP CONTEXT : The workshop was an attempt to explore the interrelationship between real-time robotics, augmented reality(A.R.), Virtual Reality(V.R.), material behavior and self-organizing generative models. The workshop focused on generating and building an agentBody structure through polymer 3D printing, AR assembly and multi-agent generative algorithms.
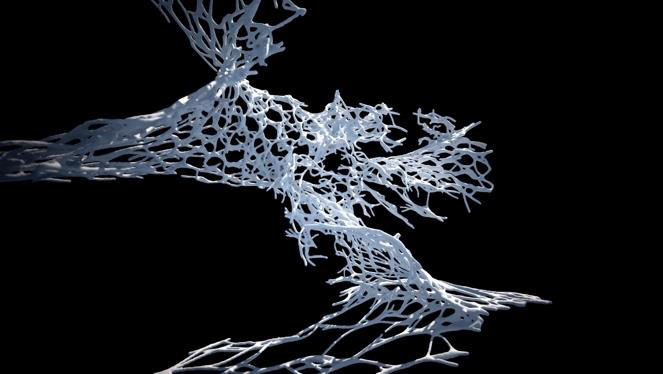
Photo : Roland Snooks – agentBody lattice (from Aalto University project)
PROJECT CONTEXT : The workshop Robotics and Mixed Reality used Kuka Robotic Arm with real time feedback to fabricate the self organizing generative model, the material used for printing was PET Pellets which were transparent and WASP Extruder tool fitted on the robotic arm. The Hololens, an augmented reality tool used to visualize and assemble the model.
TEAMS: The complete process was divided into following 4 group due to complexity : Design, Fabrication and Reinforcement, Assembly the Model and Real Time Feedback. i was part of the Assembly Team and we worked on the following task:
The first task assigned to the assembly team was to come up with a technique to attach the AR markers to each of the components in a similar fashion. So that each component can be referenced in the 3D model in the correct position and orientation as the actual structure in the physical world using the HoloLens.
The next task then was coming up with a methodology of attaching the different components together to form up the overall final structure.
The assembly process was done using HoloLense that provided a realtime reference of the exact position of each components informing the whole assembly process.
DOCUMENTATION AND VIDEO : Also there was no team Assigned for the Documentation and Videos, So from 3rd Day onward when we start production and assembling the structure, i took responsibilities of Video footages and documentations. We used parrot bebop 2 Drone to take the top view for the video and at the end compiled the whole process and make a video for the Final presentation as guided by Prof. Roland Snooks. All the Videos footages and Photographs then uploaded on drive as instructed by Natalie Alima.
Throughout the week, i captured the photos and videos to document the whole process, following were the activities and my observation during workshop from the Design, Fabrication and Reinforcement, Assembly the Model and Real Time Feedback teams
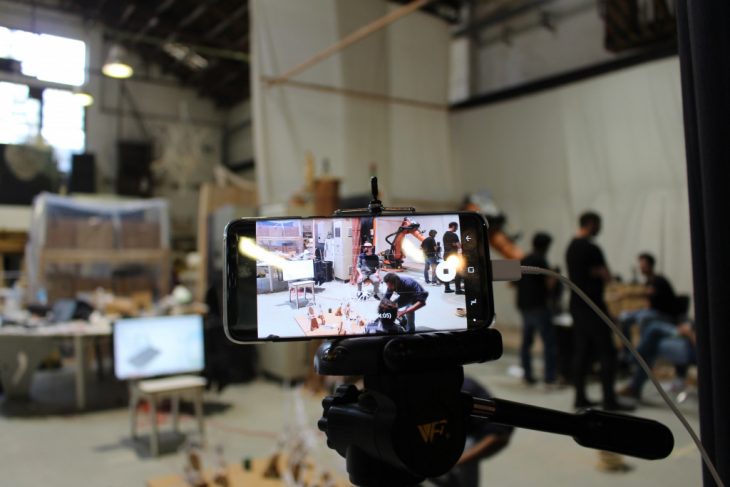
Photo : Documentation and Video Process
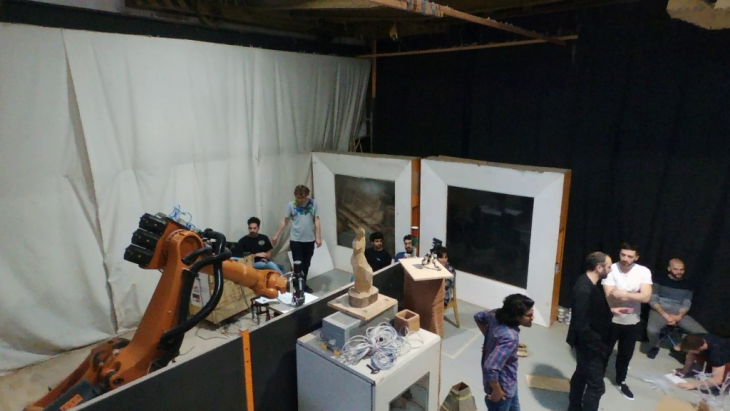
Photo : Parrot bebop-2 Drone flying to captured the Printing and Assembling Process top view
The Structure was designed by Prof. Roland Snooks and Natalie Alima.
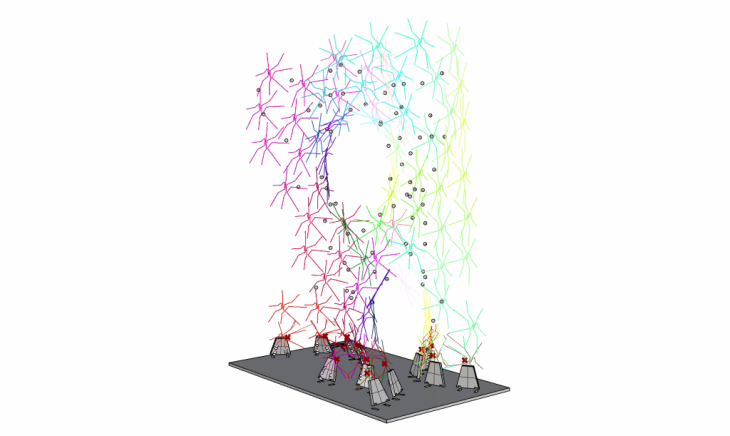
Photo : Structure was designed by Prof. Roland Snooks and Natalie Alima
The design team was tasked with unraveling and printing the components of the agent body design on a flat surface. The first attempt of printing made by KUKA-LBR-iiwa-14, with a reach of 820mm, can be guided through the path manually and re-run the same for extrusion. but this eventually failed due to technical issues in the robot control.
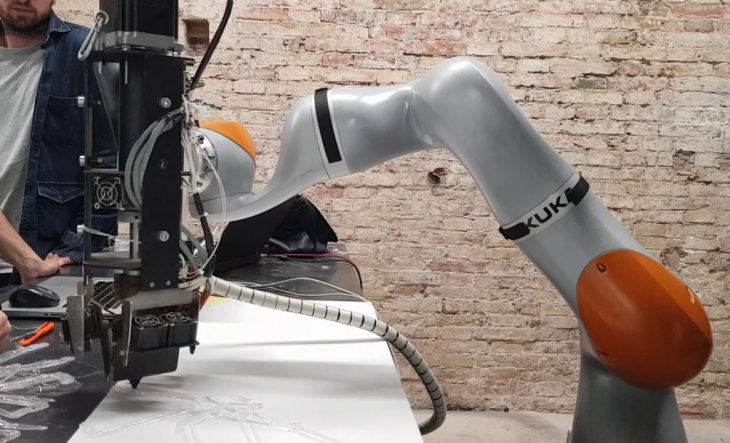
Photo : First attempt of components printing made by KUKA-LBR-iiwa-14.
The failure of KUKA-LBR-iiwa-14 printing, we moved to KUKA-KR-150 for printing the components, which is in reach of 3m that can cover for much bigger batches of cells to be reinforced.
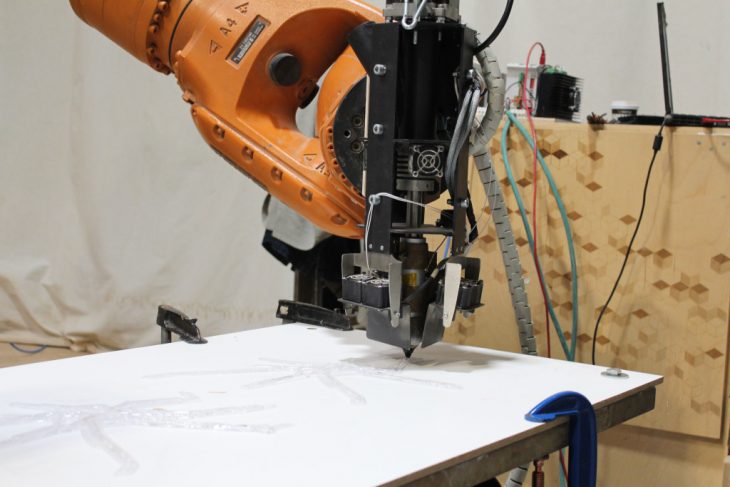
Photo : KUKA-KR-150 for printing the components
The Printed components then tagged with Aruco markers and assembled by visualizing in the Hololens by our assembly team.
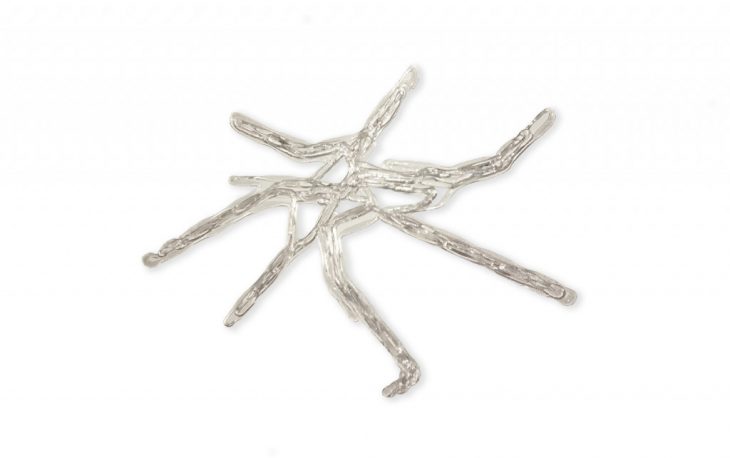
Photo : 3d Printed component
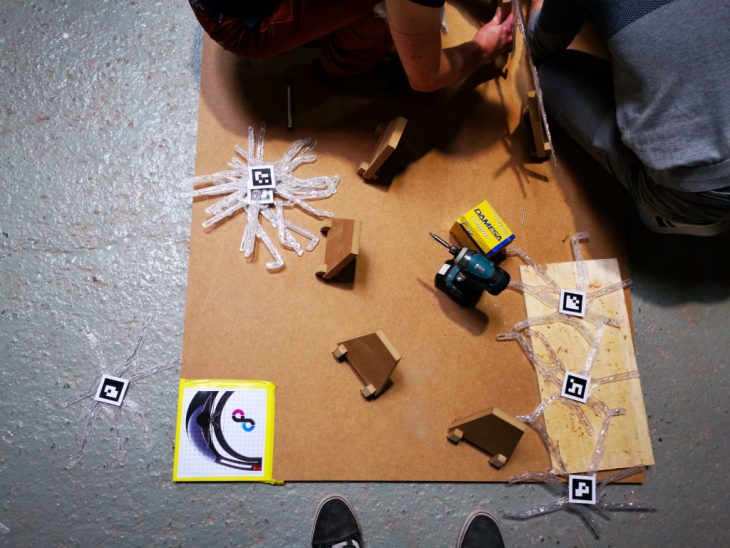
Photo : 3d Printed components with Aruco markers tagging and assembling
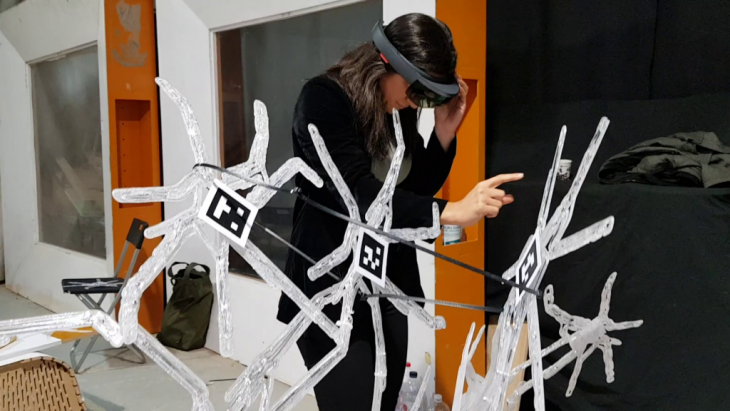
Photo : Hololens to help visualize and identify the path for assembling.
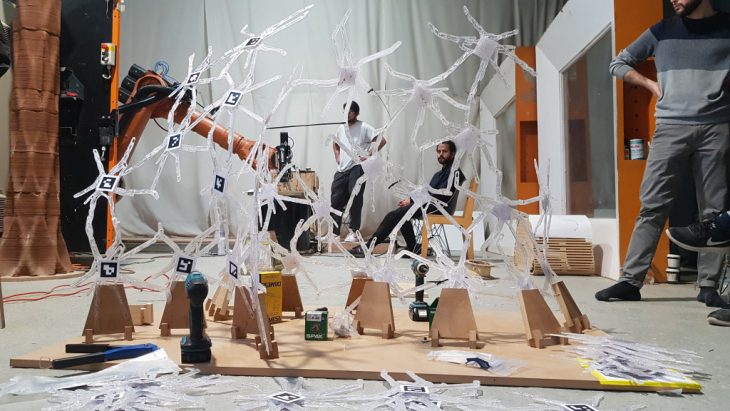
Photo : 3d Printed components Assembling in progress
The reinforcement team was tasked with generating a toolpath for the robot to reinforce the geometry by printing along the stress lines of the model. This would ensure structural stability. Owing to the complicated nature of the geometry, the Hololens was used to help visualize and identify the path along which the robot would print. An Aruco marker was positioned on the points along the path and using the Hololens the points were tagged and feed into the grasshopper simulation. These points then became a polyline which became the toolpath for the extruder to move along.

Photo : Reinforce the geometry
The feedback team was to develop a system to print the reinforcement on the model with the help of a sensor that would scan the surface and update the position of the print nozzle using a real time feedback mechanism.
CHALLENGES : In the assembling process, the main challenge to supporting the model as it was growing and preventing it from collapsing before it gains its strength from the final geometry.
Also the plastic components were either too brittle but strong or too elastic but weak. Something that required a back and force fine-tuning with the 3D printing team to come up with optimum layer thickness and width suitable for the assembly process.
The fact that any small error in the assembly quickly builds up to become a much bigger error in the higher levels. Making it not aligned with the virtual model used to inform the assembly process.
Another difficulty of aligning each component in real life with the virtual version of it in the HoloLens. Orientating components was difficult as the model in the HoloLens had tens of other components all packed next to each another, making it difficult to identify which is which and what is the correct configuration of each component.
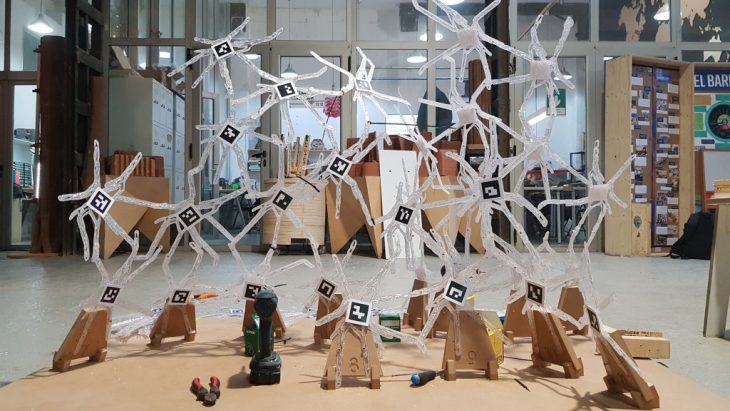
Photo : The main challenge to supporting the model as it was growing.
FUTURE STEPS : The error accumulating in the assembly could be tackled by integrating a realtime feedback using the HoloLens of what is actually built with reference to the original model. Then regenerating the remaining portion of the model with regard to the physically built portion.
Integrating structural simulation in the Assembly sequence could help in coming up with a studied sequence that would help having the structure stable and balanced as it is growing.
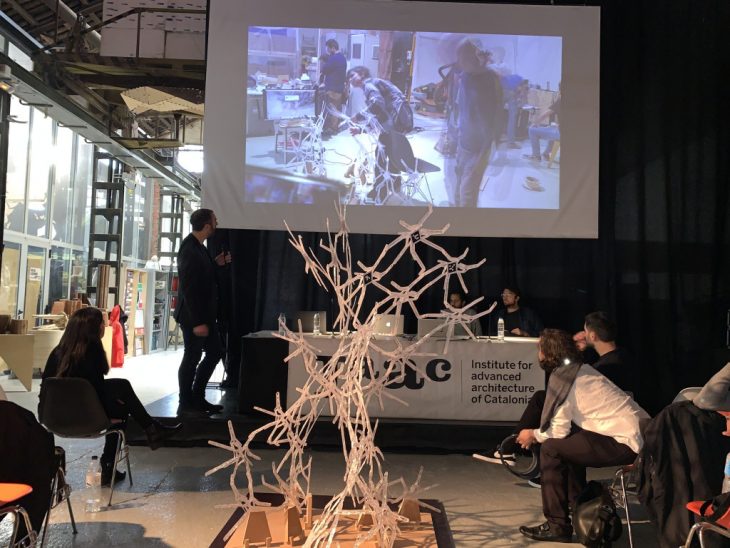
Photo : Presentation by Roland Snooks on Final Output from the Workshop.
CONCLUSION: Despite its challenges, the workflow throws out some interesting strategies that can help further digital fabrication strategies. Scanning the elements and assembling, we are able to update the 3d model considering human error and other variables.
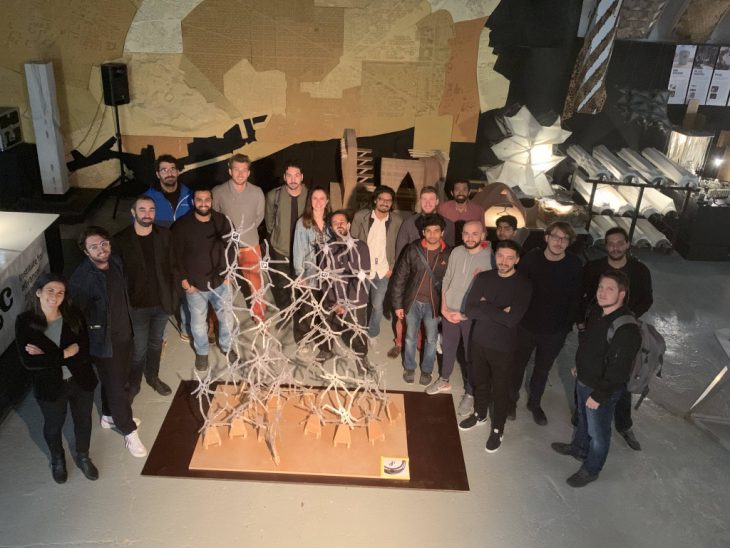
Photo : Final Output from the Workshop, IAAC Faculties and MRAC Students.
ROBOTIC AND MIXED REALITY is a workshop conducted of IaaC, Institute for Advanced Architecture of Catalonia developed at Master in Robotics and Advanced Construction (M.R.A.C.) in 2019 by,
Students: Subhash Prajapat
Faculty: Prof. Roland Snooks, Natalie Alima, Kunaljit Chadha