Context of the course
The aim of the course is to explore the design opportunities arising from three common digital fabrication processes: Laser Cutting, CNC milling and 3D Printing. The assignment consisted of an iterative exploration of each technology and material, going through a conceptual and prototyping process of design. The common framework of each exercise was to develop modular recursive geometries that can be stacked and assembled. The students were asked to deconstruct their abstract three-dimensional recursive geometries into tangible and spatial realities
Fabrication process 01 // 3D Printing
For the 3D Printing, the chosen geometric modules had to be deconstructed into a stick and node model. So that the final models could be fabricated using the 3D printed nodes and fibreglass rods (2mm diameter).
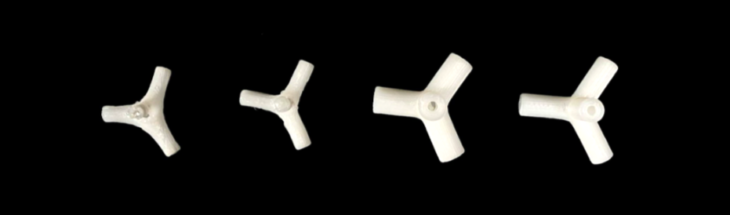
Exploring different machine settings and geometry tolerances led to multiple iterations of the nodes.
The final geometry is made up of stacked and rotated hexagonal grids, creating a strong lattice structure.
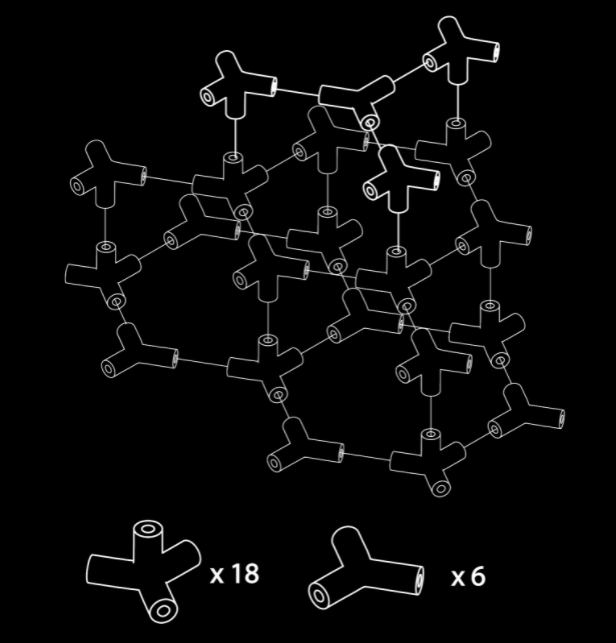
Catalogue of parts.
Total number of nodes: 24 (37)
Total length of rods (cut): 1240 mm
Internal node diameter (modelled): 2.3 mm (2 – 2,4 – 2,5)
Node wall thickness (modelled): 1.2 mm (0,8 – 1,6)
Total print time: 3h22 (5h42)
Total material quantity: 9,45 m – 23g (41g)
Material type: Z-ABS 2
Machine specifications: Zortrax M200 (M200 Plus)
Layer thickness: 0.19mm
Support type, angles and specifications: Automatic – 30° (20 – 40)
Infill type, percentage, & pattern: Normal – 20% (30) – Rectangular
Seam: Normal – Random
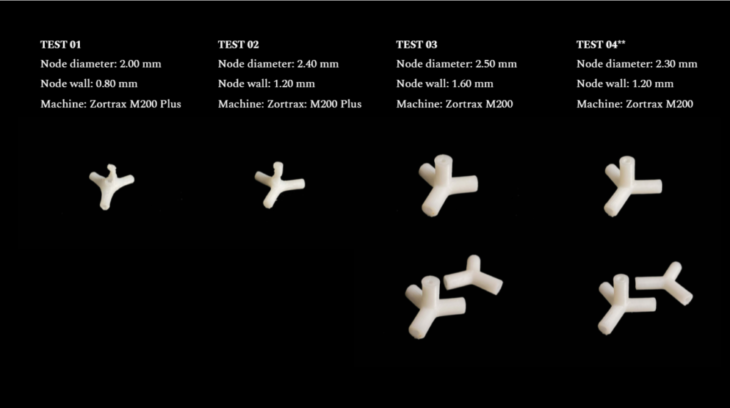
4 different prototypes were tested over 6 different printing sessions.
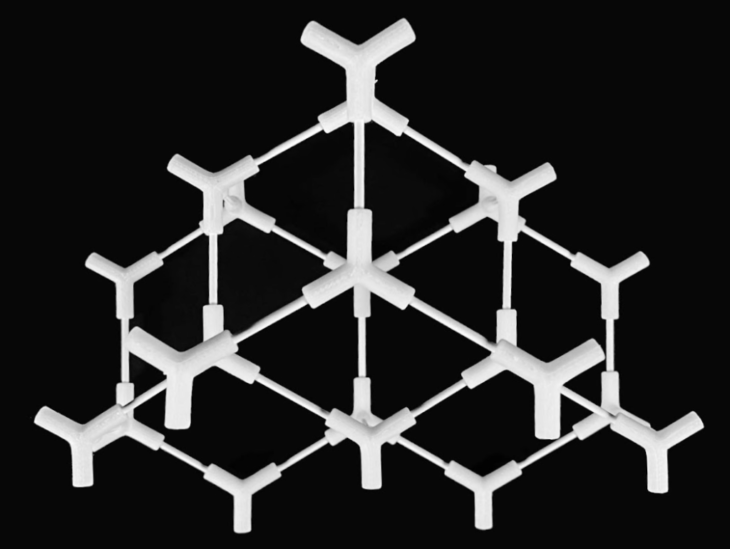
Top view final model.

Close up, final model.
A final aggregation, showing the recursive growth potential of the module was made using the Wasp plugin for Grasshopper.
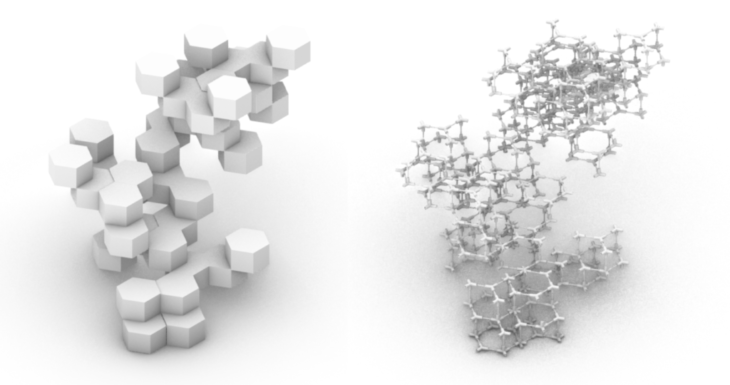
Recursive aggregation.
Fabrication process 02 // CNC Milling
An Ephemeral Capture In An Ever Growing Process
We are inspired by the intricate life mechanisms of nature. By the means of CNC milling, we are able to modularize a small prototype snippet of the plants’ life. At the same time, this helps us explore the advantages as well as the limitations of CNC.

Recursive patterns in nature.
Material: MDF
Machine: ShopBot
PostProcessor: ShopBot_MTC
Workpiece volume: 220 x 220 x 40 mm
CNC Milling Strategies
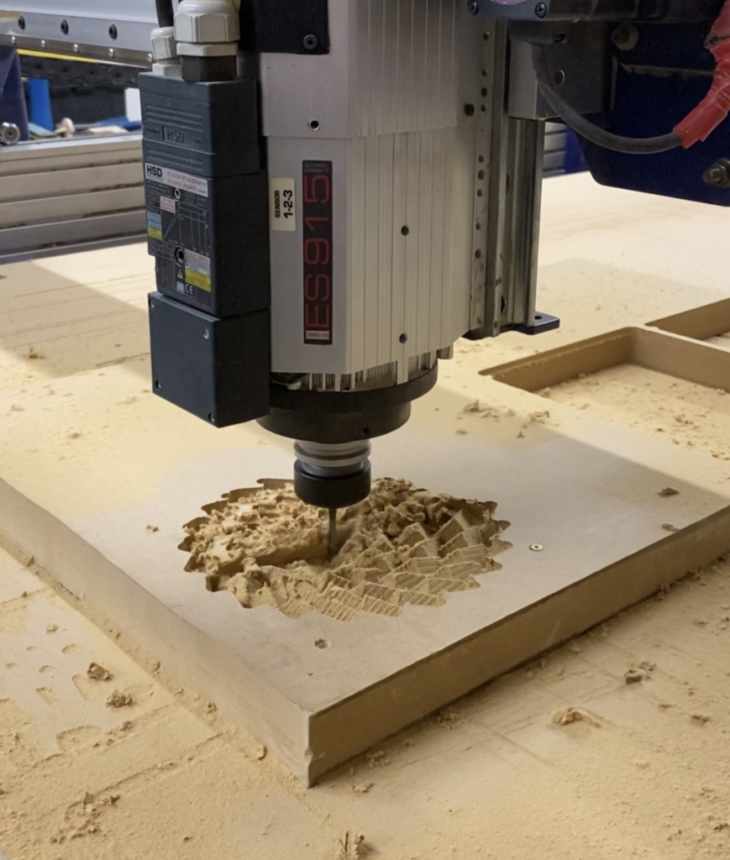
Milling process.
Horizontal Roughing
Flat Mill
Flute: 2
Diameter: 10 mm
Spindle Speed: 12000
Cut Direction: Mixed
Stepdown Control (dZ): 50%
Stepover Distance: 50%
Total mill time: 10 min
Parallel Finishing
Ball Mill
Diameter: 6 mm
Spindle Speed: 12000
Cut Direction: Mixed
Stepover Control: 25%
Total mill time: 13 minutes
Axis Profiling
Flat Mill
Diameter: 6 mm
Spindle Speed: 12000
Cut Direction: Up-Cut
Stepover Control: 0%
Total mill time: 6 minutes
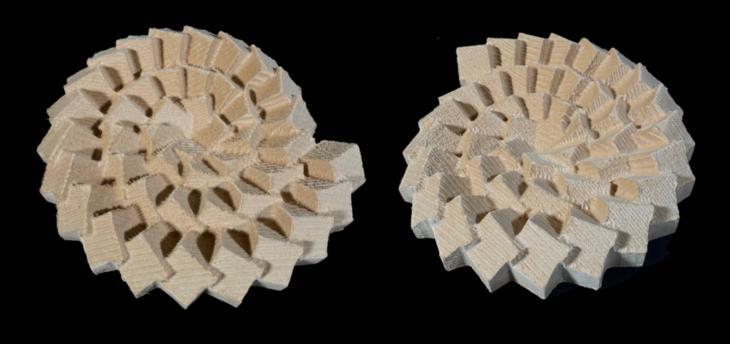
Finished model.
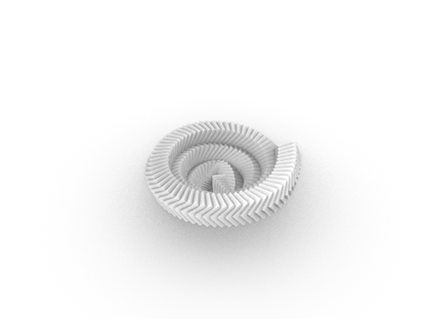
Spatial aggregation of the pattern.
Fabrication process 03 // Laser Cutting
For the laser cutting prototype, white Polypropylene 0.5mm was used to test the bending properties of the material and the technique. Based on the Undulatus project (2015) by the Architectural Engineering Department at the Vrije Universiteit Brussel, a recursive module is designed to grow into a larger curved surface.
Different material thicknesses were tested before defining the final one (1.2mm and 0.5mm). The thinner one was more accurate because of the size of the pieces and the folding angles. Once the final thickness material was defined, different values for engraving (speed and power) were evaluated.
Two different 2d shapes were designed to build 3d volumes by folding them. The design of the joints and different tolerances for the interlocking parts of the model were tested before defining the final pieces.
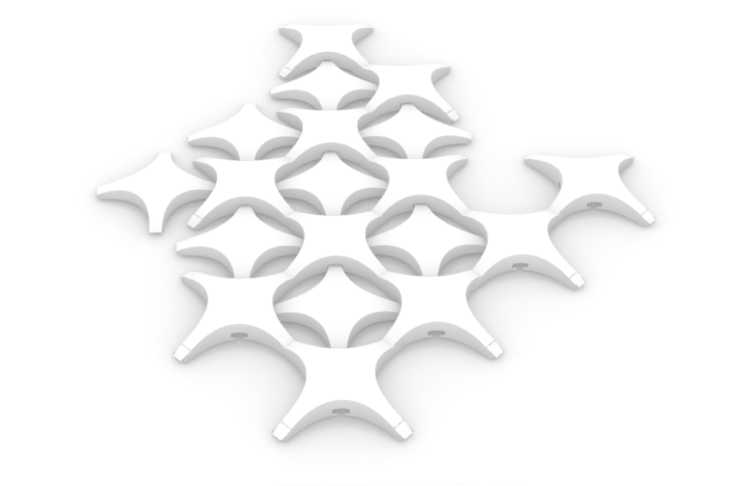
Interlocking geometry.
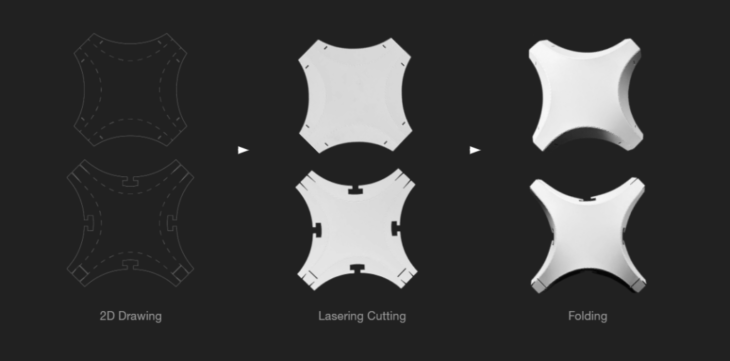
Prototype development.
Finally, the four legs of each volume have tapered cut in the curvature, and two of them have a slit on the top face too. The height of the interlocking is the principal value that affects the final shape.
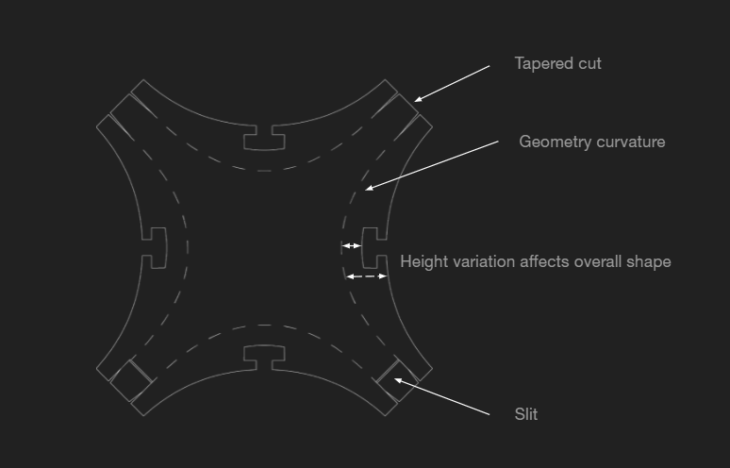
Shape/curvature defining factors.
The purpose of the design was to define a flexible 3d volume capable of reproducing a curved recursive geometry. Within the design, we were able to build different volumes using different amounts of pieces.
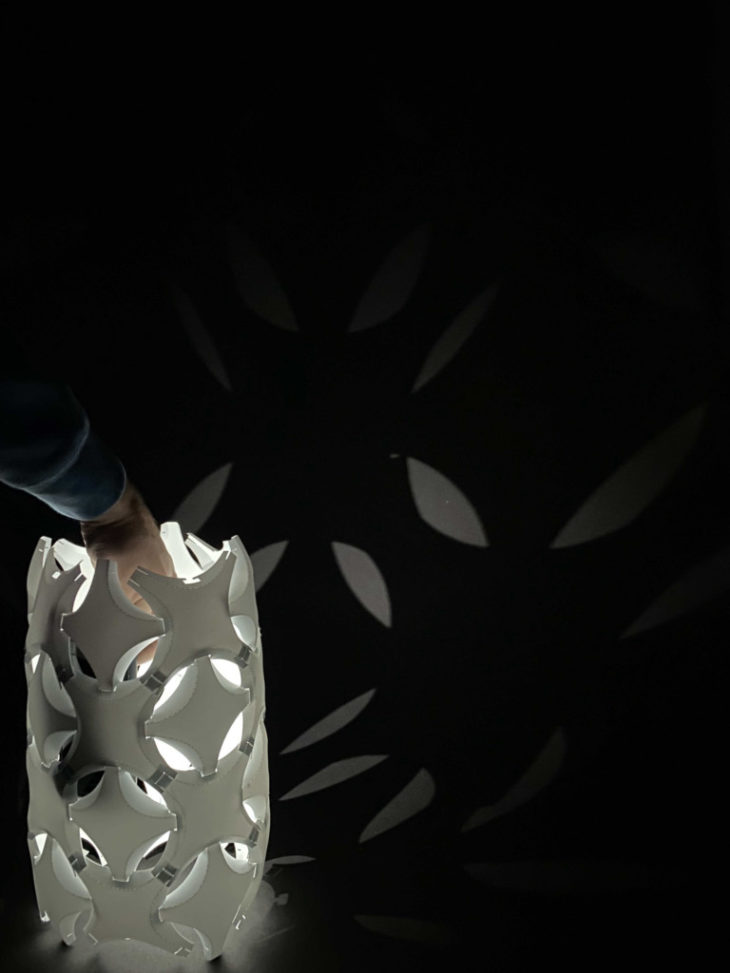
Final model.
Recursive Geometries – G19 is a project of IAAC, the Institute for Advanced Architecture of Catalonia, developed during the Master in Advanced Architecture (MAA01) 2021/22 by students: Jett Demol, Marta Navarro López & Yue Wu; faculty: Ricardo Mayor, Lana Awad, Shyam Francesco Zonca & Marielena Papandreou.