Material Cycle For Wooden Urban Furniture
Circular Design in the Built Environment
– Understanding buildings as material banks
How to design ?
Discovering tools and strategies for how you can implement a design for disassembly and deconstruction
A building Life Cycle
Project overview
The Goal : Intervention on the streets around Sagrada Familia to enable Pedestrians and Tourists to have a holistic experience during the visit.
The Objective : To design an adaptive and changing landscape with Urban “Stuff”, that allows variations, Adjustments and testing. The entire design process is based on Circular design techniques and mindful selection of materials and their lifecycle.

Streets around Sagrada Familia
Reference projects
Superilla – Sant Antoni
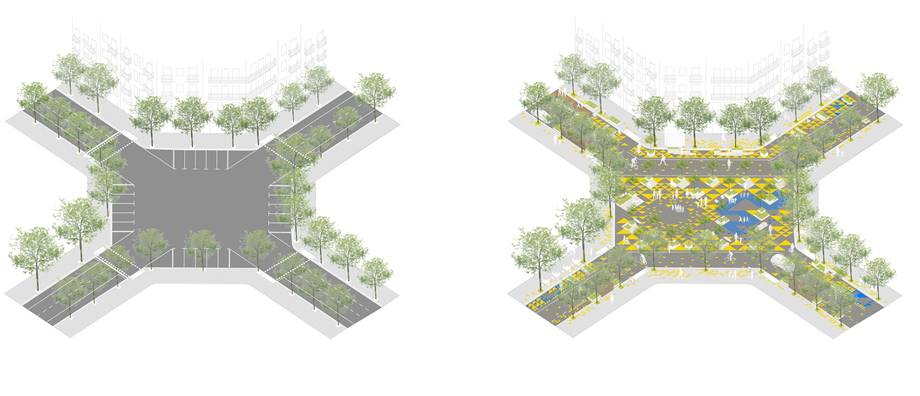
Sant Antoni street view
To create a Superilla grid which will –
1.Limit vehicular movement, resulting in increased pedestrian access.
2.Reprogram uses, reorders mobility and draws a new landscape without modifying the existing urbanization.
3.Organise the streets around Sagrada Familia for a better touristic experience and creates an opportunity for a dynamic neighbourhood.
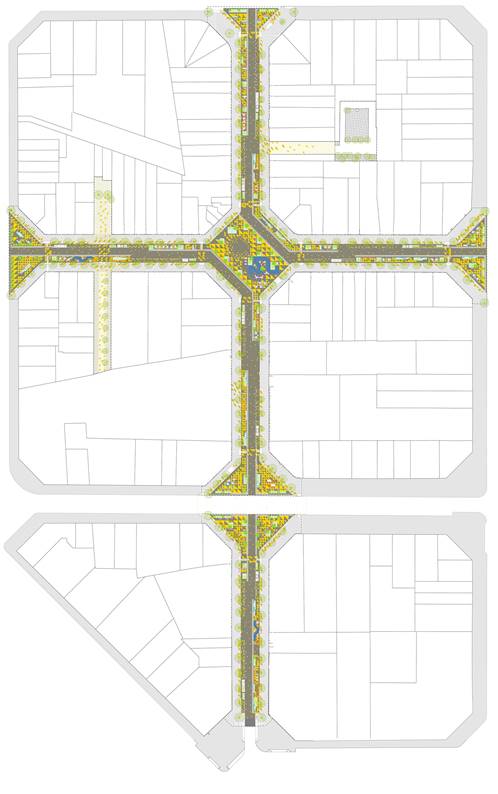
Sant Antoni street plan
MQ Seating – Vienna
To design an Urban furniture module which is –
1.Easy to Assemble and Disassemble
2.Change configuration and create different spaces and seating types.
3.Fits into the Superilla grid
Process of Design for Disassembly
The Following are the steps taken for the design of Urban furniture –
1.Material research – To find materials which satisfy the circularity criteria. 5-6 year lifespan.
2.Finalise the material based on the criteria such as Carbon footprint, Durability, End of life, etc.
3.Design the furniture module w.r.t configuration possibilities.
4.Data on emissions and Carbon footprint at each stage of the material, from manufacture – Re-use – Dispose.
5.Assess the Material on birth to death criteria. Optimising the second life and end of life plan.
Forests of Europe
Much of Europe’s forests lie predominantly in the northern latitudes or on the periphery of the mountainous regions of central and southern Europe.
The most extracted softwood species in 2017 were: 3,62,106 m3 of radiata pine (Pinus radiata D. Don), 3,40,106 m3 of maritime pine (Pinus pinaster Ait.), 1,36,106 m3 of Scots pine (Pinus sylvestris L.) and 0,55,106 m3 of Salzmann pine (Pinus nigra Arnold subsp. salzmannii (Dunal) Franco).
SHORTLISTED WOOD TYPES
– SAWN TIMBER
Pine wood timber
Spruce wood timber
–PLYWOOD
Poplar plywood
SAWN TIMBER
Log preparation
The branches and bark are removed from the tree trunks.
Removing the bark leaves all the heartwood, and most of the sapwood.
Processing
Logs are stockpiled under water sprays to prevent them from splitting as they rapidly dry out.
The logs are then sawn into rectangular shapes.
Logs are fully saturated and the saws leave a rough surface on the wood, as some of the fibers are torn out rather than cut.
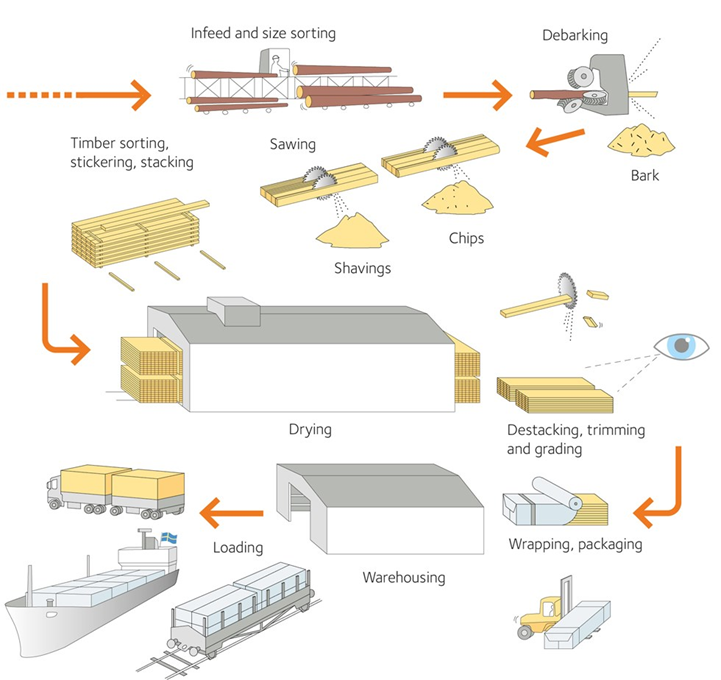
Timber manufacturing process
Seasoning
When a tree is felled, it contains a large proportion of water / moisture. Many felled trees have forty to fifty percent water content. Seasoning of natural wood, is the process through which excess water / moisture is removed, leaving typically fifteen to twenty percent water content.
Natural Seasoning
By water By Air
Artificial Seasoning
Electrical seasoning Chemical seasoning Kiln seasoning
At the sawmill, the logs are cut into ‘boards’ using equipment such as circular saws and bandsaws.
This is called ‘conversion’. The first stage of conversion is a process called ‘breaking down’, which means rough sawing.
The second stage is called ‘resawing’ and refers to more accurate / precise cutting and finishing, such as planning and further machining.
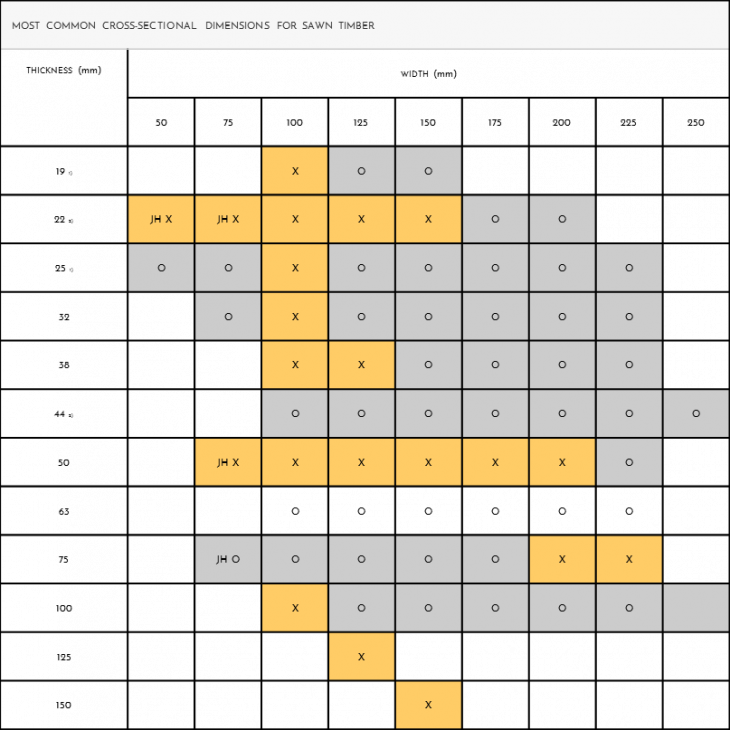
1) usually pine 2) usually spruce JH = usually done by splitting afterwards, whereby the width is 2 mm less that the nominal size x =standard size o = rarely produced size
Spruce / Properties
-popular for the furniture industry, papermaking, packaging and construction.
-The wood is soft, low in weight and has medium density
-has a small resinous, high resistance to cracking
-warm and light wood tones.
-great resistance to moisture.
-Painting, coating and staining does not cause problems.
Pine / Properties
– medium weight
– relatively soft
– strength elasticity are good
– heartwood has good natural durability except where it is in direct contact with earth or moisture
– It has a high natural moisture content
– The coloring only affects the appearance, not the physical properties of the wood.
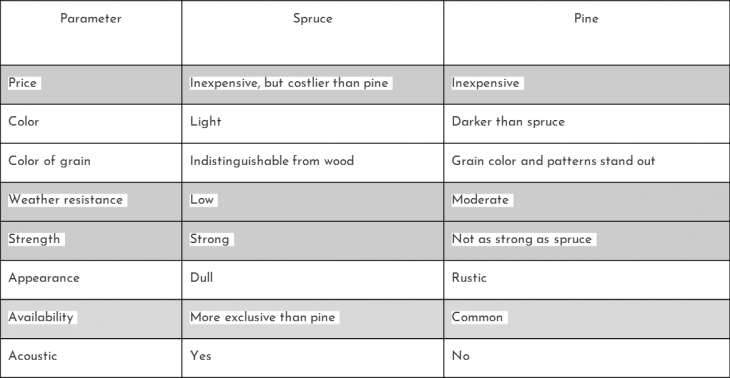
Comparison between Spruce and Pine
SAWN TIMBER – IBU EPD – EGGER
Dry board raw density average –
Spruce – 420 kg/m3
Pine – 480 kg/m3
Application
Decorative and constructive purposes.
Strength-graded timber may be used for load-bearing building elements, e.g., in structural engineering, both as individual element or as lamella in a glued element, such as e.g. glue-laminated timber, plywood, or finger-jointed solid structural timber.
Manufacture
The production takes place therefore in the following
partial steps:
- Log sorting
- Debarking
- Machining, profiling, sawing,
- Timber
- Marketization
Environmental and Health during use :
No risk of water, air or ground contamination.
No health hazards or effects.
Extraordinary effects :
Fire
Building material class B2 “normally flammable” according to DIN 4102-4
Fire class D-s2, d0 according to DIN EN 14081-1 Fire protection Name Value
Building material class D
Burning droplets d0
Smoke gas development s2
Water
No hazardous water contaminants are washed out.
EGGER timber is not resistant to permanent exposure to water (standing water).
Re-use phase
In case of renovation or demolition, EGGER timber can be selectively removed and used for the same application or a different one.
Given the high calorific value of about 16 MJ / kg, energy utilization in approved plants for the generation of process energy and electricity as part of cascading use is reasonable.
Disposal
Resulting material waste as well as those from demolition activities are to be reused primarily as material. If this is not possible, they must be channeled into energy recovery. Disposal is not permitted. The waste code according to the European Waste Catalogue is EAK 17 02 01.
SAWN TIMBER – C2C – ACCOYA WOOD
Accoya wood is a high performance wood designed for outdoor use and challenging applications.
Tree – Pinus Radiata
Cradle to Cradle
Material health – Platinum
Overall certification – Gold
End of life
Biodegradable
Compostable (100%)
Recyclable (100%)
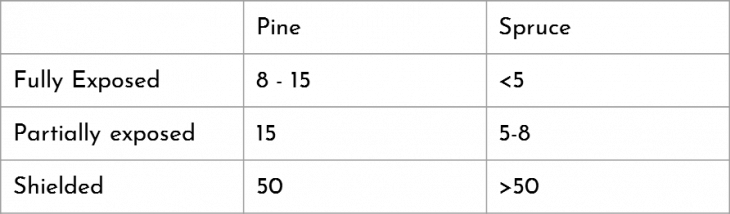
Lifespan of Pine and Spruce
Engineered timber
Plywood
Properties
-Easy to install
-Resistance to creep
-High resistance to impacts
-High resistance to weathering
-Doesn’t swell in humidity
-Versatile
Plywood variants
-Hardwood plywood
-Softwood plywood
-Marine plywood
-Medium Density Overlay (MDO)
-Baltic Birch plywood
-Tropical plywood
-Pressure treated plywood
Glue types
–Urea formaldehyde : Plastic resin glue, Hardwood plywood bonding, Reliable, Moisture resistant, Can be toxic in interiors
–Polyvinyl acetate : Water and high-temperature resistant, Edge jointing and veneering
–Melamine formaldehyde : Hard, thermostatic plastic, Waterproofing (on top of urea formaldehyde), Decorative purposes
–Phenol-formaldehyde : Weather resistant, Exterior applications, Not as good as urea formaldehyde for plywood & particleboards
–Resorcinol-formaldehyde : Similar to phenol-formaldehyde, More expensive
–PureGlue : Non-toxic, Formaldehyde- free, Resin + soy flour
Exterior plywood finishes
–Paints:
Acrylic latex paints: flexible, resistant to cracking
–Water repelling coats:
Polyurethane varnish
Water-based stains
Water sealer: doesn’t block all the pores
Plywood production in Catalonia
-Wood panels production has been on the rise
-Expansion of production facilities
-Main uses: furniture, doors, construction & flooring
Plywood product // EPD: Poplar plywood
-PureGlueTM
-Non-toxic
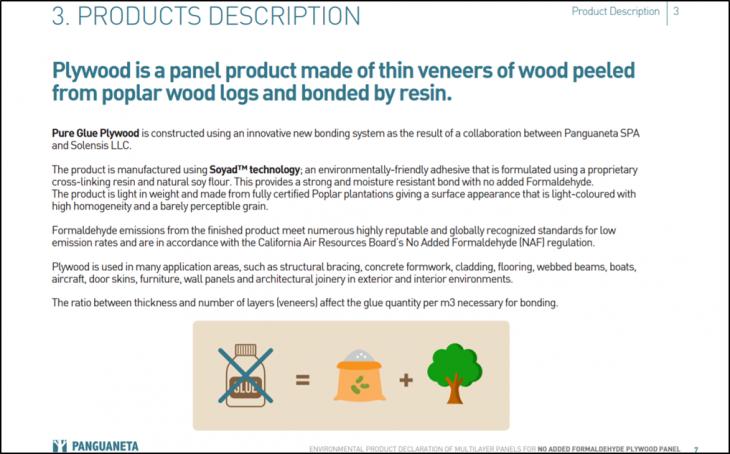
EPD: Poplar plywood
-Thickness 20mm
-9 layers
-400 m2 glue per m3
Amount of sequestered CO2:
522.7 kg CO2-Eq. / m3
Total plywood volume:
26.4 m3
TOTAL SEQUESTERED CO2:
13,800 kg CO2-Eq. / m3
Producers & Distributors
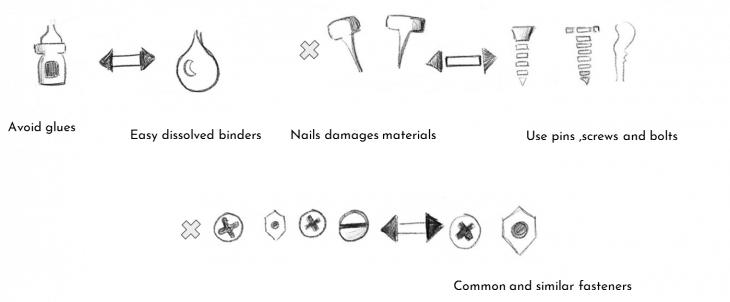
Connection strategies
Proposal
Plywood end of life options
-Reuse in projects (eg furniture making) > secondary market
-Crushed and transformed into particle board
-Incineration for energy production
-Decomposition
Deconstruction plan
1.
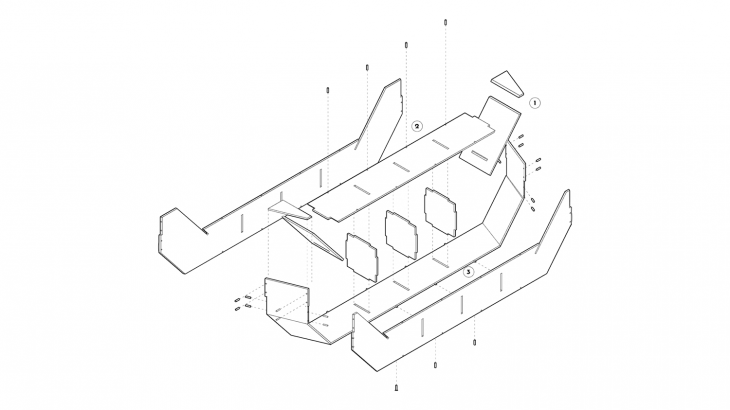
Wood after usage
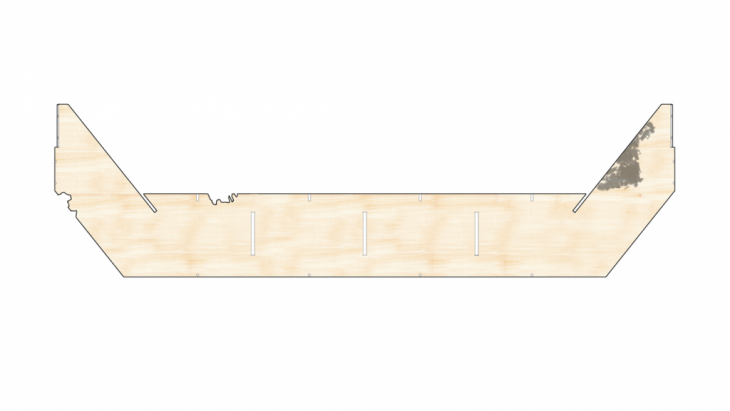
Possible damage areas
Gaps
-Lack of local EPDs
Barriers
-Lack of advanced secondary material market
Opportunities
-Increased local wood panel production
-Lack of local EPDs
-Lack of advanced secondary material market
Material Cycle For Wooden Urban Furniture is a project of IaaC, Institute for Advanced Architecture of Catalonia developed at Master in Advanced Architecture by Ashwin Parandhaman, Rana Ibrahim, Prarthana Sudhindra, Christos Trompoukis