MANYFORMS explores the idea of a employing a unique smart material that can be created out of everyday objects onto an architectural system that is easily replicable anywhere on site. Heat actuated nylon muscles are cheap and quick to make, and have the capability to be produced en masse, for systems employing their character at various scales. Changing the parameters, or hacking the fabrication process results in a vast array of springs with different properties, suited for different tasks.
Actuated at 60-75°C, these muscles contract by up to 10% and are capable of carrying 700 times their own weight and have no reported loss of strength over multiple cycles, thereby making them ideal to use on an architectural scale. Since one of the preconditions for actuating these springs is a calibrated amount of tension, MANYFORMS explores systems that work with a careful counterbalancing of forces by pairing the springs so they tense each other, and create movement when one is actuated. While optimizing the amount of work the muscle has to do, such systems add the capability to create a member that can be aggregated to twist, turn and lift – much like the human spine – in multiple axes and directions.
These can then create shape-shifting systems which can be controlled to span across spaces in a dynamic and configurable fashion, allowing a large degree of control over the creation, construction and use of these systems.
The phenomenal scalability that this material provides has been used to form different parts of the system. We can create members that can be carriers of compression or tension to form a larger dynamic system. The force flows that are created can be relayed live to tiny elements which hold the main struts together to create a dynamic system that feeds back on data from its own structural state, thus creating systems that are not only dynamic, but configurable to the extent of being capable of handling the fluctuating forces generated in dynamic architecture.
MANYFORMS is more than a product, it suggests a larger idea that can enable dynamic architecture systems at varying scales, over millions of cycles with a fabrication process that can be taken to any location, facilitating configurable, manipulated architecture.
Fabrication Methodology
Turning a nylon string to a nylon muscle requires a number of pivotal steps, influencing overall performance of the final product. Each step is understood as a part of a hackable process. The process is hackable in its ability to purposefully dictate the final product by choices made during the fabrication process.
The following section, in tandem with the subsequent section, showcases the fabrication parameters discovered during the course of the studio and the resulting performance of the nylon muscles.
Two different fabrication processes were explored during initial material testing. To create a Type II nylon muscle, first the nylon muscle must be brought to the moment just before overtwist. When it is just about the overtwist, the spring is wrapped around a rod. A threaded bolt was used for experimentation as the threads provided a bed for the spring and eased the fabrication process. Once the nylon string is threaded around the rod, it is clamped on each side and then heated past the glass transition temperature. This deforms the spring into a muscle, and heats it into a new shape. Although Type II nylon muscles have larger coils and significantly greater contraction percentages, they are not able to carry significant weight. As the goal of the studio was to develop a novel architectural system, Type I nylon muscles were predominantly used.
As can be seen in the table and the graph below, the strain or contraction percentages had a specific range dependent on the type of muscle tested. The weight was maintained constant for each nylon muscle diameter. The weight for family of nylon muscle were determined on an observational basis. For instance, the weight was added until the muscle began to unwind when actuated. Although 1.2mm nylon muscle were able to carry a significantly greater amount of weight, the contraction percentage was less than the 0.6mm nylon muscles with the 1.2mm family contracting on average 4.85% and the 0.6mm family contracting on average 6.14%.
As a result, for prototyping, 0.6mm nylon muscles were used. The greater contraction percentages would allow for observable changes to occur and more complex systems to be developed. However, the contraction percentages recorded were observably far lower than those quoted by the University of Dallas at Texas. Fabrication methodology or heating distribution at the time of recording may be at fault and could have affected observed values.
Actuation
Nylon muscles require a temperature greater that 47 °C to contract. Additionally, the entirety of the muscle should be heated uniformly to ensure optimal contraction occurs. Therefore, a distributed and controlled heat source had to be included incorporated into the eventual design of the architectural system. Resistive heating using nichrome wire was eventually concluded to be the most appropriate choice, however, other resistive heating elements and a coolant system were also tested.
The most successful heat actuation method used, and further prototyped, was threading the nylon muscle through brass tubing. The brass tubing was then wrapped in insulating kapton tape. Afterwards, ten loops of nichrome wire were wrapped wound the kapton tape and then covered with another layer of kapton tape. Any tubing could potentially work as long as it is able to heat quickly and then dissipate heat quickly. Nichrome wire generates heat very quickly from relatively low voltage values.
Additionally, threading the nylon muscle through the tubing allows for even distribution of the heat, resulting in an even actuation of the muscle. If the entire muscle is heated, then the contraction percentage is increased as all coils are compressing, rather than only in select areas.
Component Evolution
The rigid component was developed for three purposes: to hold the heating element, to keep the nylon muscle in tension and, lastly, to act as the foundation for the architectural system. The key performance parameter for design was the angle between the two elements. The angle is a result of the contraction percentage of the muscle. The component is balanced on either side with two identical nylon muscles. When cool, the nylon muscle acts as a typical spring and is able to stretch. As discussed in previous chapter, when heated the nylon muscle contracts between 4 – 10%. The component holds both springs in tension, and is able to flex at each joint based on the actuation system. Each joint is controlled by two lengths of nichrome and brass tube. Theoretically, each joint would be controlled separately based on an input.
Moving towards 3-dimensional movement required a new type of module and a new type of system. However, the logic remained the same. The modules needed to be able to supply adequate tension in the spring, while allowing for movement at the joint. To achieve the required, and eventually greater, angle changes, a ball joint was introduced into the system.
System Explorations
3D Curves
Initial explorations were focused on the creation of a curve. The input parameters were consistent with the prototype: a single element design and size, and a common snap angle. A line was drawn and the creature begins to crawl along the line, creating a line of best fit. Fitting the drawn line is an approximation, as the snap angles are a parameter which dictate direction. At each joint, there are potential for four choices. Distinct 3D curves are created based on the direction of the component at each joint.
State Shifts
State shifts refers to the transition from one form to another. The members created by the nylon muscles change form based on heat input. Each joint has a potential for four directions. As a result, if one joint changes direction, then the form will change. Linking these joint changes together creates a programmed set of movements.
Multiple Members
Exploring not only single line state shifts, but multi-line state shifts allowed different shapes and geometries to be explored. The first types of exploration were interested in individual members which began as separate entities, becoming defined shapes.
The states shifts of each member to reach these types of forms was also explored as structural integrity and weight requirements of the muscle were key performance parameters to be understood.
Future Potential
The future potential of the system is numerous in number, with a range of different areas which could be explored for different explorations. For instance, multi-scalar components, multi-scalar members, connections and locking mechanisms, multi-modal actuation (such as passive actuation, temporal actuation, structural stability and scale, energy consumption, carrying capacity, nylon integrity (protective casings), component materiality, secondary materials and user interaction.
The following image showcases different spaces which could be created by hanging numerous of the linear elements together. An interactive and temporal wall is created in this instance.
Weaving differently sized elements together can infer the potential to increase structural stability of the system as well as light diffusion.
With past design and geometric explorations, the anchor points for the members have been numerous, with each member in the agglomeration having its own distinct anchor point. As each member state shift, the anchor points remain in a constant location. The following design iteration imagines a movable creature, with a fixed anchor point for all members. As state shifts occur, the creature is able to move.
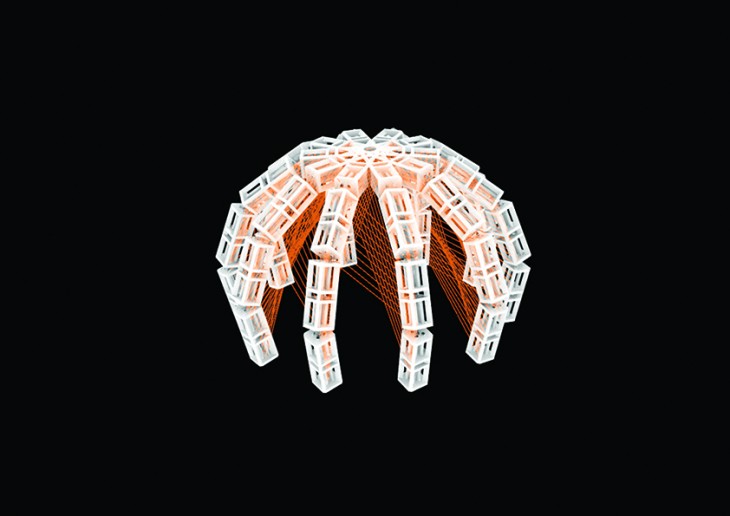
Shift State 1
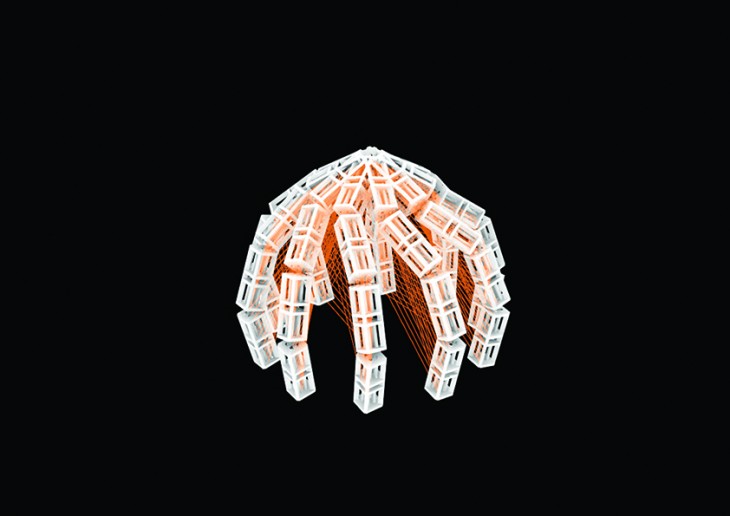
State Shift 2
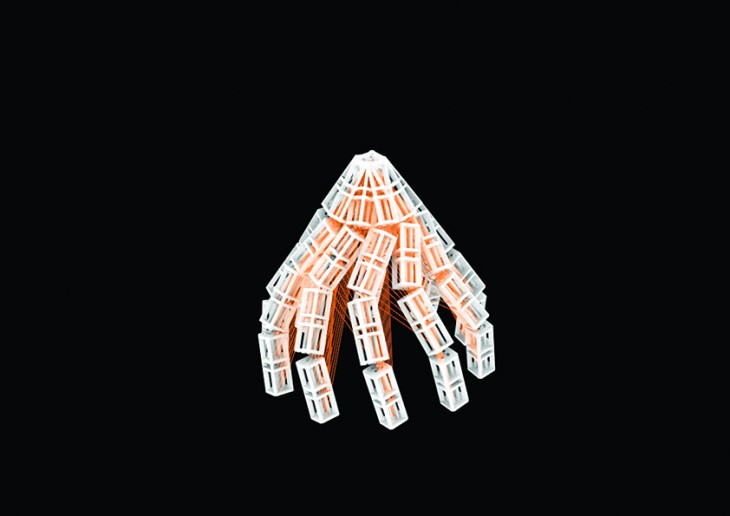
State Shift 3
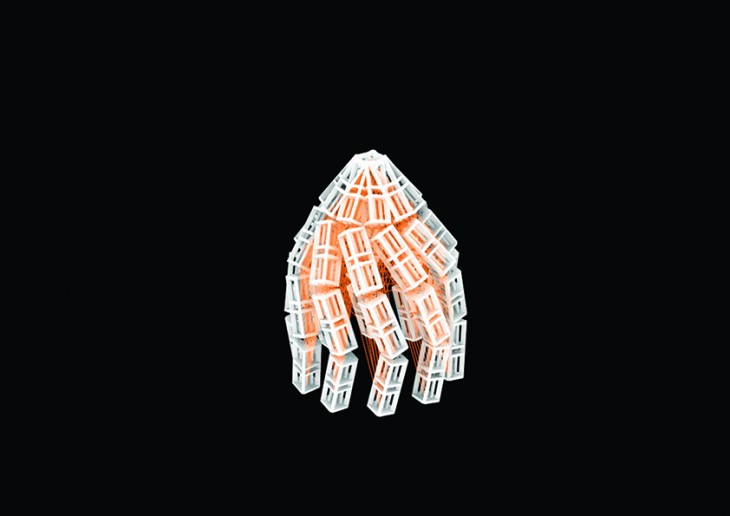
State Shift 4
Interface
The interface for MANYFORMS is an interactive virtual reality design tool. Using the VIVE, a head mounted virtual reality screen, the user can paint and draw 3D curves. These curves are populated with design elements. By using the interface, a plethora of different geometries and shapes can be explored and tested in a virtual environment.
MANYFORMS is a project of IaaC, Institute for Advanced Architecture of Catalonia developed at Master in Advanced Architecture in 2016 by:
Students: Utsav Mathur, Jean Sebastian Munera and Connor Stevens
Faculty: Areti Markopoulou
Faculty Assistants: Alexander Dubor and Angelos Chronis