Curved Cross-Laminated Timber
This project leverages the naturally occuring deformation in timber to create self-shaping curvature in cross-laminated timber (CLT) panels. By taking advantage of the plain sawn cut – and thus consistent grain patterns, as well as the hygroscopic properties of the green (freshly cut) wood – which has a high moisture content – a subtle, yet consistent curvature known as cupping forms as the wood dries.
Offcuts salvaged from milling waste piles were selected based on grain pattern and viability as members within the panels. These were then processed, into straight pieces of consistent thicknesses allowing them to both fit neatly together during the pressing process and re-expose the fibers to their surrounding air.
Scientific interest
Green wood
Wood has two main characteristics which are important to understand for this project. Firstly, it is a hygroscopic material; meaning it absorbs water when in contact with it, as a liquid or vapour. It always contains moisture, and green wood has a much higher moisture content than seasoned wood. As it dries, wood undergoes an anisotropic distortion. This means that the dimensional changes in the three directions (Radial, longitudinal, tangential) are unequal.We try to take advantage of these dimensional changes, which have different motions depending on the end grain pattern.
For making a single-curved wood panel, the end grain pattern we are interested in is when the growth rings are curved up or down. This is achieved by doing a plain-sawn cut. When there is a change in moisture (from high to low), the lamella (long piece of wood) will want to cup.
The system
Say we get a few plain-sawn, green lamellae and join them side by side, with the same grain orientation. We will call this the active layer. We then cross-laminate a thinner, dryer layer on top, called the passive layer. In the drying process, the change in moisture of the active layer will cause the active layer lamellae to cup. We end with a bilayer we can consider self-shaped.
We now have a single curved bilayer panel, with no additional formwork or brute force needed, and thicker layers than veneers, typically used in complex wood panel shaping.
Green wood processing
Curvature prediction
After processing the material, several studies were conducted on individual pieces to measure moisture content, environmental temperature and humidity, thicknesses, and the role these parameters played in informing a final curvature once the wood reaches a stable moisture level. Using these inputs, the project explored several methods to help model and predict this curvature, namely: machine learning, Timoshenko beam theory, and finite element analysis.
Fabrication
After two weeks of seasoning, the panels were milled into their final form using a 6-Axis Kuka KR150 mounted with a router. To scan and calibrate the work pieces, several methods were explored – including photogrammetry, 3D mapping using the motion-controllers equipped with a VR headset, and ultimately using the robot arm itself to model the 3D geometry and generate the toolpaths.
Robotic milling setup
Design + Assembly
The prototype’s helical design takes the form a developable strip – a geometry in which double-curvature is achieved through the manipulation of a flat object. The panels – which comprise a cylindrical section are cut diagonally from corner to corner and reoriented along their consistently arched edge. The various panels are connected along their flat edges and ordered to maximize the overall curvature. The hardware connecting the panels holds the overall form in suspension.
Connections and hardware
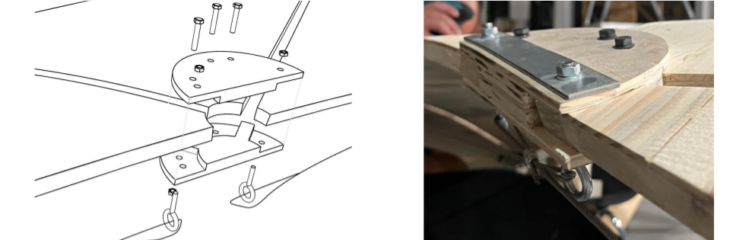
Tolerances, Turnbuckles & Adhoc Engineering
Possible applications
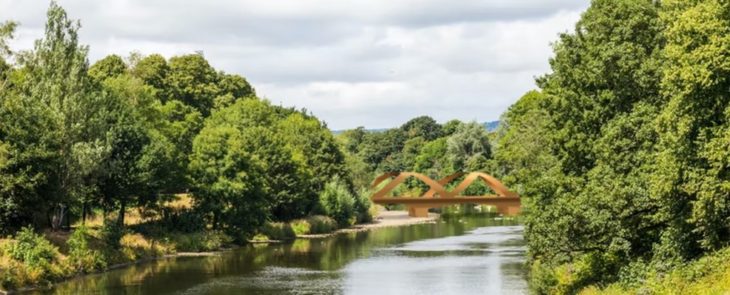
Render of possible application
Curved Cross-Laminated Timber is a project of IAAC, Institute for Advanced Architecture of Catalonia developed at Master in Robotics and Advanced Construction, in 2021/2022 by:
Students: Michael Blackburn, Libish Murugesan, ?pek Attaro?lu, Jordi Vilanova
Faculty: Alexandre Dubor, Marielena Papandreou