[[Cube] in a Cube] // WORKSHOP 3.1
The aim of this workshop is to define a design strategy for a space frame to be fabricated from robotically bent rods with the final design to be informed by machine learning. During the workshop, the group of [[Cube] in a Cube] defined the design to be described by two cubes within a single cell, having the outer cube to be defined by a overall shape-giving global geometry, the spaceframe, and an inner cube within each cell which has the allowance of rotation around all three axis and a change of scale. Eventually, a neural network was trained to predict the rotation and scale of the inner cubes of the final space frame to be structurally sound within the given global shape.
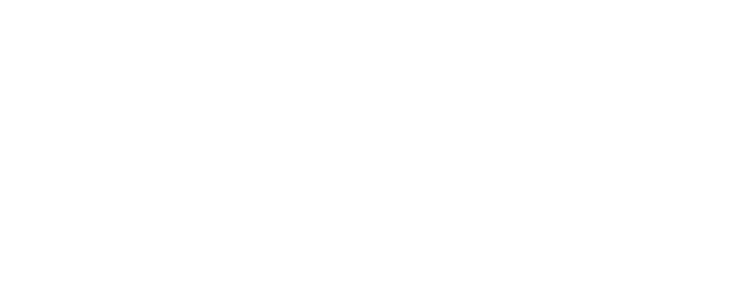
Concept Diagram
Overview
The workshop started with manual explorations to get comfortable with the continuous rod and the possible topologies and connections for a single cell and the form-finding of a global geometry.
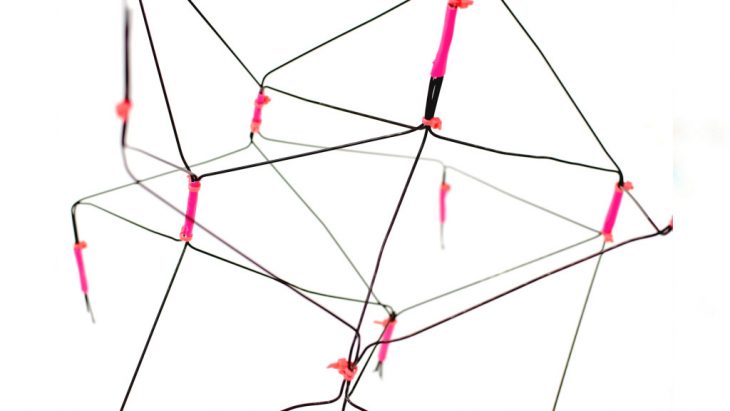
Manual Explorations
Preparation of the Dataset
The necessity for a cell geometry to be parametrized with only a few variables as changing parameters led to the development of the idea of the cube in a cube concept.

Evolutionary Solver
Local Cell vs. Global Shape
During the process of structural optimization of the global shape, several concerns had to be addressed. The cells of the firsts version were missing a kind of cross bracing to prevent from folding inwards. The overall global shape, in general, was too ambitious and the structural analysis with karamba3D was not promising.
Iteration Version I
The updated 2nd Version includes an improvement to the overall shape of the spaceframe and an updated concept for the inner connection of each cell. But it had still the potential for improvements.
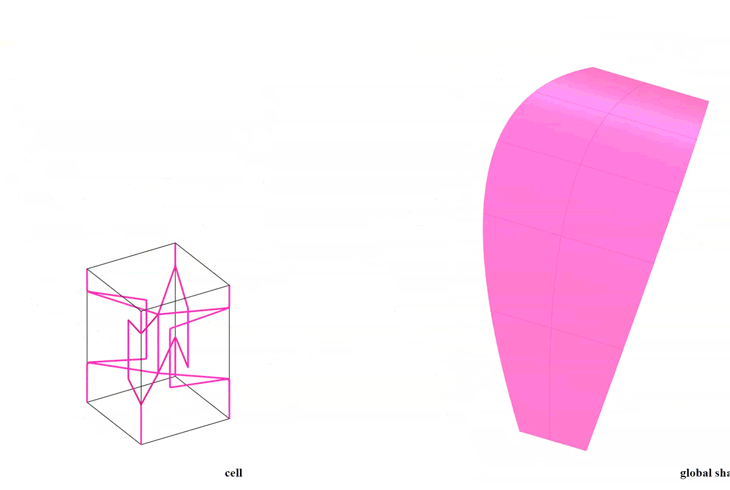
Iteration Version II
The 3rd iteration finally promised to give good results in simulation globally and locally. An additional central connector to the inner cube was introduced to secure a sturdy structural system.
While a part of the group continued to work on the finalization of the digital part of the project, the other half was starting to prepare the first set of toolpaths for the robotic bending of metal rods. A first full-size prototype of a single cell with the cube in cube topology was fabricated.
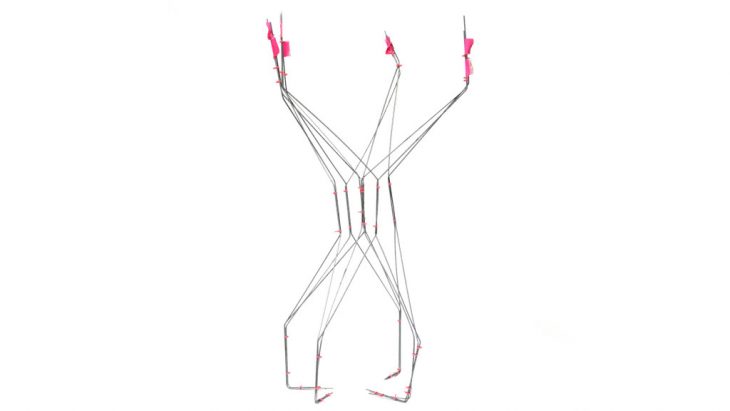
First Full Size Prototype
Training the Neural Network
By having created a parametric model of the cube in a cube cell it was possible to generate a large dataset of different shapes and dimensions for the outer cube acting as a bounding box of the cell. These were used to find the optimized values for the scale and rotation of the inner cube of each outer geometry with the use of karamba3D and the Galapagos evolutionary solver.
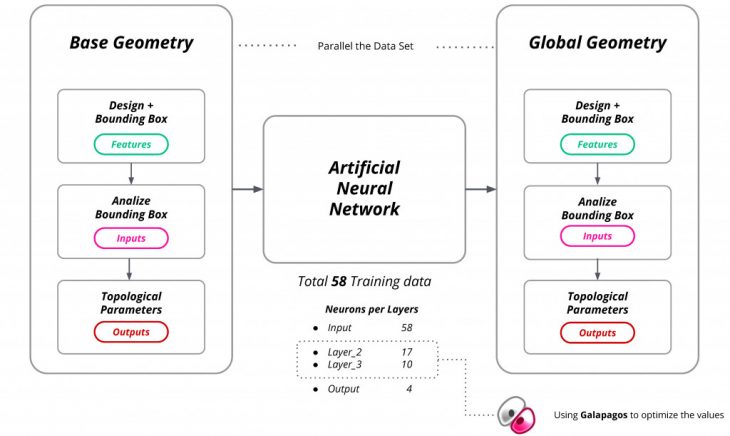
Machine Learning – Structural Prediction
The values were written down into a dataset to start the training of an artificial neural network. The neural network, once trained, can be used to predict the behavior of each cell instead of the time-consuming structural analysis and was driving the design of each cell in our final global geometry.
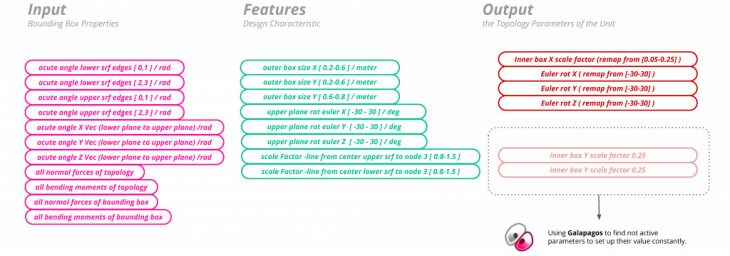
Dataset
Besides the values necessary to define the parametric model of the outer cube as input for the neural network, several values of deformation from the karamba analysis were saved to the training data. The rotation and scale to define the inner cubes were saved into the same data and were used as the training output of the neural network, as this is what the neural network is meant to predict for the final shape.
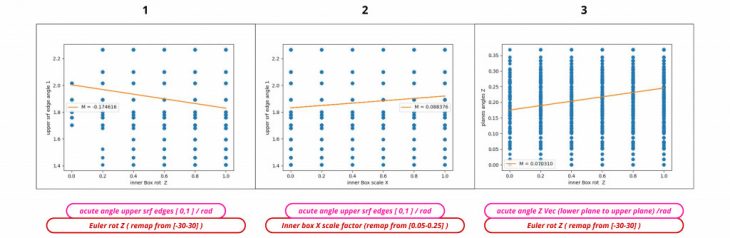
Most Influential Values for Structural Behaviour
Structural Analysis
Before fabrication, the global geometry was tested one last time in entirety and adjusted accordingly with the use of karamba3D in grasshopper.
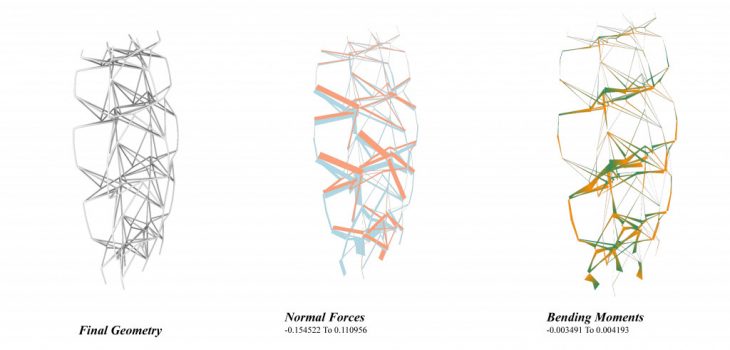
Structural Analysis of the global Geometry
Fabrication
The ABB 140 industrial robot was equipped with a custom end-effector for the robotic bending. Certain fabrication limitations had influenced the final design. Especially the concept of the connection from cell to cell had to be adjusted last minute to allow for a collision-free movement of the toolpath in simulation and the resulting robotic fabrication.
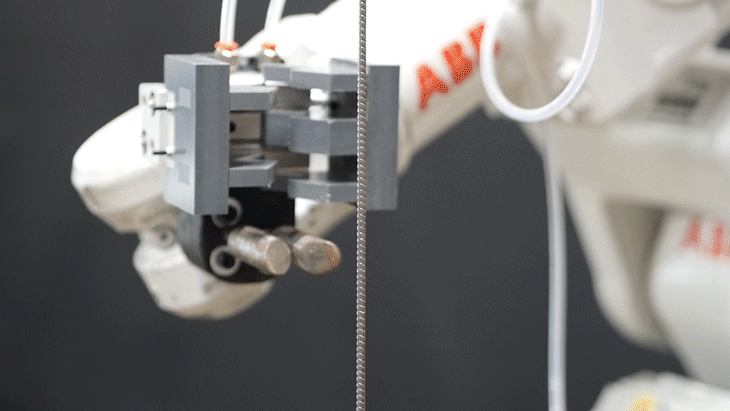
Robotic Rod Bending
Assembly
The assembly strategy was to start with the outer rods which could be folded into a single shell already standing upright and filling the cell with the inner rods which are then forming the inner cube geometry and finally holding the entire cell in shape.
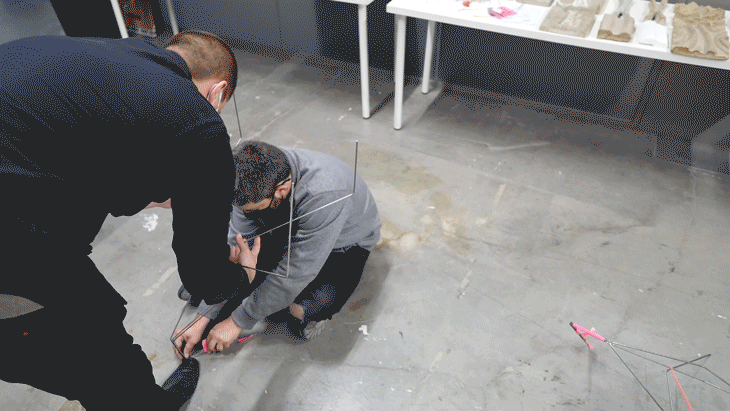
Assembly
The cells were mounted onto a ground plane and stacked on top of each other in a two by two spaceframe. Within the timeframe of five days for the workshop and just the last two days for the final production, 12 rods per cell and a total of 48 rods of around 1,5 meters were robotically bent to fabricate the final prototype.
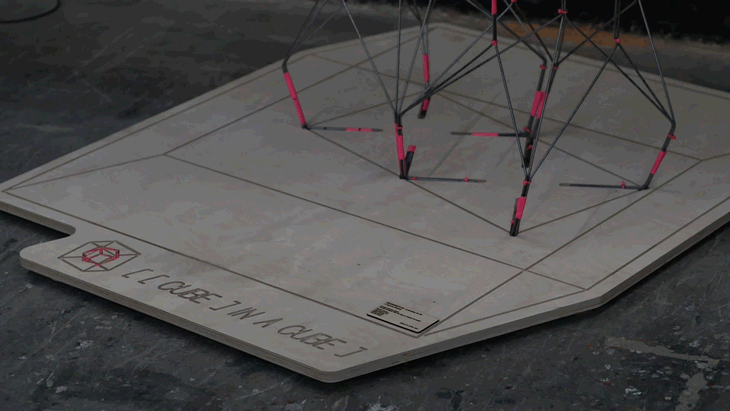
Final Spaceframe Model
Video Documentation
Click here or on the image below to watch the Video Documentation of this workshop.
Cube in a Cube // W.3.1 is a project of IAAC, Institute for Advanced Architecture of Catalonia
developed at the Master in Robotics and Advanced Construction in 2021 by:
Students: Shahar Abelson, Hendrik Benz, Charng Shin Chen, Helena Homsi, Aslinur Taskin
Faculty: Zeynep Aksöz
Faculty Assistant: Ashkan Foroughi, Ricardo Mayor
Workshop Participants: Shahar Abelson, Hendrik Benz, Alberto Browne, Charng Shin Chen, Michael DiCarlo, Helena Homsi, Arpan Mathe, Juan E. Ojeda, Orestis Pavlidis, Aslinur Taskin.