Forty per cent of world’s carbon emissions are produced by the construction sector, within which 8% is from producing cement. There is an urgent need to mitigate carbon emissions to stay beneath a 1.5 degree global temperature increase.
What if construction materials absorbed carbon emissions instead?
We wanted to investigate materials that provide an alternative to some uses of concrete, and have ‘carbon-negative’ properties. A carbon negative material is one which absorbs more carbon dioxide across its lifecycle than is emitted in its creation. They are also referred to as having negative embodied carbon, or being carbon sinks.
Three state-of-the-art projects constructing with carbon negative materials:
1. Material: hempcrete
Hempcrete is a biocomposite construction material made of hemp shiv (the stalk of the plant), powdered limestone and water. It both absorbs CO2 when growing as hemp, and continues to absorb it after its composition into hempcrete. If appropriately situated, this means it can continue absorbing CO2 after construction. Industrial hemp absorbs 8 – 15 tonnes of CO2 / ha of cultivation. Data on how much CO2 is absorbed by hempcrete does not yet appear to be standardised.
Aside from this, it is lightweight, low density, and has excellent moisture absorption and thermoaccoustic properties (37-45 dB sound absorption). It can be used in RCC structures for external walls and internal walls – although not for load bearing structures. It has good fire resistance, is non toxic, does not offgas and can be returned to the natural environment at end of life, including for use as fertiliser.
State of the Art: Flat House, by Practice Architecture
An attempt to ‘grow’ a UK family home using hemp crop cultivated on the same land on which the house is built. Its creation is a prototype for offsite pre-fabricated sustainable hemp-based construction, a characteristic that enabled it to be constructed in just 11 months, and across winter, when hempcrete building can be problematic due to damper weather. A hemp-based bioplastic was also used in sheets to clad the outside of the house, made of outer hemp stem fibres bound with a sugar-based bioresin. The house had some higher embodied carbon elements, such as concrete foundations, but was still calculated to have a net absorbtion of 5 tonnes of carbon.
2. Material: fly ash
Fly ash constitutes 60-88% of the by-product generated by combustion from coal-fired power plants.
0.75 – 1 billion tons are generated annually.
Less than 30% is reutilized, usually as fillers in brick manufacturing and road or dam construction.
Even though the use of coal for energy generation is declining, countries with massive coal reserves such as China and India continue to depend on it to meet their ambitious development goals.
If left unchecked, Fly ash which contains trace amounts of toxic substances such as arsenic, mercury and lead, ends up leaching rivers and lakes, greatly harming wildlife and agriculture.
Fly ash can be used as a carbon sink in CCUS technologies, and while it does absorb some carbon from the atmosphere when in brick form, the amount is minimal compared to when it is used as a substrate and mixed with other compounds.
State of the Art:
Construction projects are mostly limited to localized residential houses and apartment buildings due to localized supply.
Designers have also proven the viability of using Fly Ash concrete in 3D printing projects, but applications have been limited.
3. Material: mycelium
Mycelium is part of the fungi that extends and branches underneath. It is an emerging low cost material that has been explored in the product design and textile industry. Depending on the material it combines with, it can be customized to replace timber, plastic, and foam. It has recently been explored in architecture as facade, self-standing structure, and bricks. These projects combine mycelium with agricultural byproducts, where the manufacturing process involves ‘growing’ of the building blocks.
State of the Art: Mycotree, by Sustainable Construction, Karlsruhe Institute of Technology
Conclusions
These three projects highlighted some interesting possibilities for carbon negative materials, and some material-specific issues that would need to be addressed to allow for a wider uptake for each of the specific materials.
More broadly, however, these innovative prototypes highlighted that the use of carbon negative materials in the construction sector is negligible. We took a step back, and re-framed our research question to throw the net wider:
Carbon negative materials exist.
They have potential as alternatives to some uses of concrete, but their utilisation is neglible.
So what are their barriers to use in the construction industry?
Observing our materials of interest on a matrix of carbon negative to carbon positive, mapped against use in the construction industry, we identified three major perspectives which could cast interesting light on our research question.
- Carbon negative materials were used little to not-at-all in the construction industry, but mostly found in a research environment
- Carbon positive materials are used to a high degree in the majority of our buildings, ie. mostly found in a construction industry environment
- Caught in the middle, drawing from research environments but under real-world pressures , we found the environment of a professional architecture practice
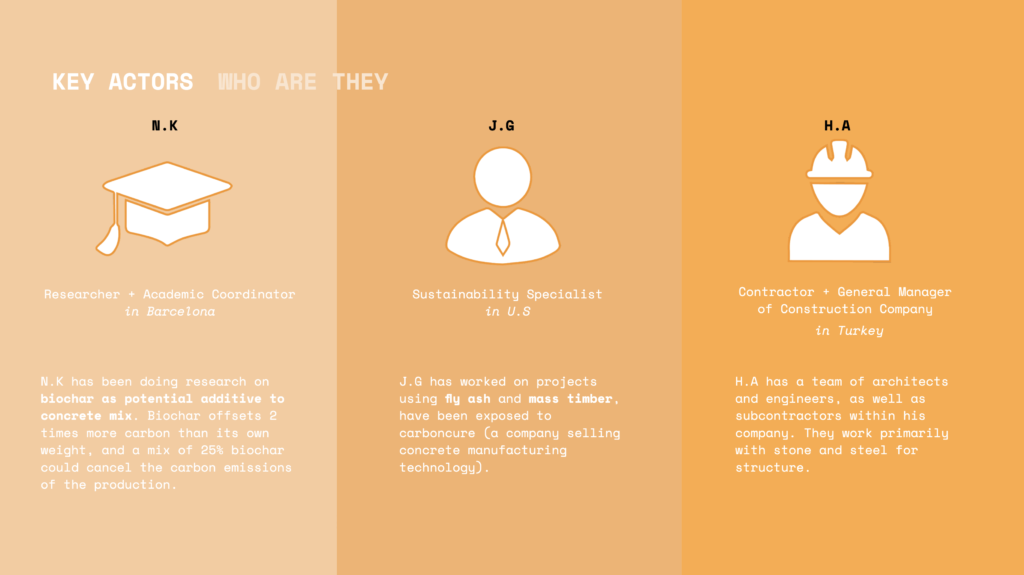
Stakeholder interviews – we spoke to three key players
We conducted stakeholder interviews to assess the barriers to carbon negative materials from each of these perspectives: ‘NK’, a researcher and academic coordinator focussing on biochar development in Barcelona; ‘JG’, an architect and sustainability specialist working in a major US architecture firm; and ‘HA’, a contractor and general manager of a construction company in Turkey.
Barriers to uptake of carbon negative materials in construction
“Obviously the best strategy is not using concrete… but that’s in an ideal world.” JG
BARRIER: communication
“Communication between design and construction is a big issue…there’s a delay factor that occurs.” NK
Different actors had different preferences in doing their research, acquiring knowledge, and iterating their design. The research field typically share their outputs in the form of workshops and conferences, whereas the construction industry prefers to acquire their knowledge via magazines, journals, and talking to colleagues. This discrepancy in how knowledge is shared encourages separation between research and construction.
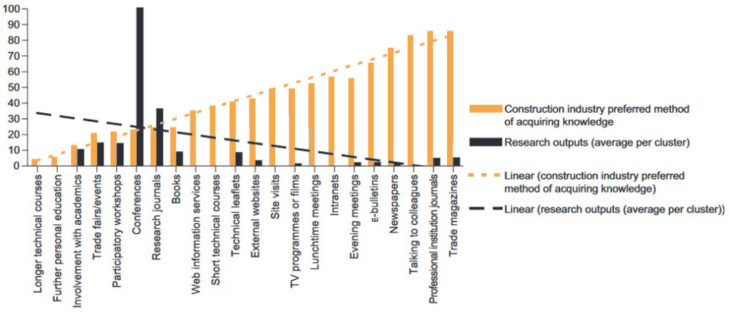
Source: Knowledge exchange between academia and industry
The three actors also had different preferences in software. The academic and research side of architecture showed preference in using Rhino and Grasshopper, whereas the construction industry leaned toward BIM programs. By using different software that do not translate fluidly, we are introducing delay factors in communication. Such inefficiency in communication could introduce miscommunication as well as poor collaboration between the research and the construction field.
BARRIER: economics
“Money talks.” JG
Contractors benefit from cheaper options, be it in material costs or production time. A new material will typically have a higher upfront cost. Unless the client can be persuaded to increase the project budget, this cost will come out of the contractor’s profit margin. Alternative materials must become a comprehensive and developed product for the subcontractors to feel more comfortable in exploring them.
BARRIER: know-how
“This is an industry that says – ‘we’ve done this well for years, why would we change?’” JG
There is a lack of familiarity with carbon-negative materials in the construction sector, and this breeds a reluctance towards their use. This contractor reluctance was identified by both NK and JG, and a lack of familiarity acknowledged by HA.
While non-contractors may attribute blame to the construction sector, it is important also to acknowledge that responsibility for the outcomes of using a new materials varies across our three stakeholders. Familiar materials are the safer choice for contractors, who carry the responsibility of making a building structurally secure.
It’s also clear to see how the difference in familiarity with newer materials across our different stakeholders could arise. Architects are required to have a standardised education before assuming their role, and the academic environment of their training provides a juncture for new material knowledge to be disseminated. In contrast, the path of education towards working in the construction sector can vary widely, and may occur on the job under apprenticeship from older professionals. Employment patterns can also be fragmented in the construction industry, and on a project-to-project basis, so there is no guarantee of uniformity of exposure. Junctures for contractors to become familiar with new materials cannot be assumed.
BARRIER: regulations
“One of the biggest challenges of using low carbon material, especially around structure, is regulation.” JG
“Softwares only feature common materials that fit existing regulations.” NK
BARRIER: conclusions
These barriers broadly hold the framework of the construction industry. It has been suggested that regulations and market demands were main instigators of change. However, confronting and overcoming any one barrier could trigger change in the other ones as they are all interconnected.
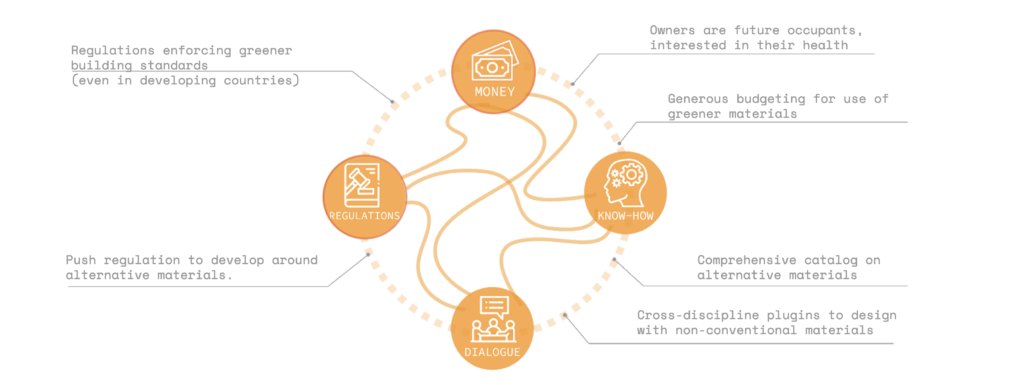
The barriers to uptake of carbon negative materials in the construction sector are varied, but interconnected.
Carbon negative materials are current used hardly at all in the construction industry. The barriers to their use seem broad and are currently impenetrable – but through their identification we are also able to identify opportunities for uptake of these materials, as well as a note of caution.
Opportunities for uptake of carbon negative materials in construction
OPPORTUNITY: Digitalisation
Digitalisation: Classification
“We attend construction fairs every year to discover new materials.” HA
Classification, digitalisation and standardisation of materials and their properties helps improve contractor confidence and increases their use.
Databases such as Mindful Materials and Material District:
- Facilitate product selection
- Facilitate new product certification
- Aggregate product sustainability information while minimizing effort on the part of manufacturers and designers
- Allow manufacturers to publish comprehensive information about their new products
Digitalisation: Material Standardisation
“Right now we make structures that are mechanically performative, and that’s all we value…I work with a matrix of performance” NK
When materials progress past the research phase and have empirical data and testing backing up their material properties, contractors are more willing to accept their use.
Companies such as Carbon Cure serve as an example where an carbon offset is being used in construction due to contractor confidence in an established product.
Digitalisation: Software & Usability
“Regulation is the biggest factor impeding new material adoption… [but] new smart buildings are being developed, and many new digital and physical tools have emerged.” HA
As CAD and BIM software have become the norm, designers tend to select materials from established material libraries. The inclusion of new materials in these softwares is critical to expand their use.
Revit already has an extensive library of concrete and steel features which facilitates their selection.
Tally – a Revit plugin – and EC3 are tools which allow for architects to create a Life Cycle Analysis (LCA) on their building to understand its total embodied carbon and long term environmental impact.
Qualitative Considerations
“Regulation is the biggest factor impeding new material adoption” – J.G.
- Lifecycle Analysis – allows shareholders to compare costs over a long period of time. Often leads to more sustainable design choices. A $600,000 initial investment turned into a $6 million saving over 25 years – West Elementary / Perkins Eastmann
- Cost shifting – Higher costs when using a sustainable material can be balanced with savings in other parts of the building
- Thorough cost analysis – Material cost is not the only factor to consider when choosing materials.
“Timber was more expensive as a material, took half the time to assemble, meaning it cost us less to build and drastically decreased the embodied carbon of the structure” – J.G.
OPPORTUNITY: Regulation
Regulation has the power to change behavior.
Some examples such as New York Local Law 971 and the Washington Clean Buildings Bill state that all building will have to comply with stringent sustainability standards such as LEED compliance or face a fine.
New regulations in France will mandate all new public buildings to be built from at least 50% timber or other natural materials starting in 20222.
The US recently approved provisions allowing for the construction of tall mass timber buildings up to 18 stories, a large jump from the current 123.
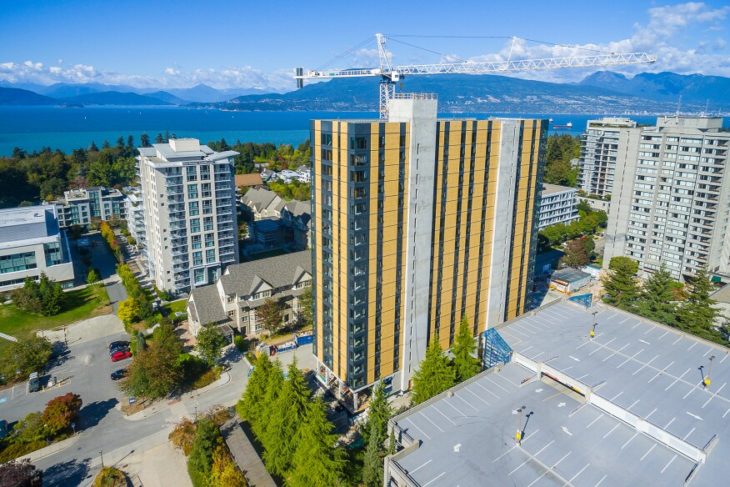
12 Story Timber Building in Vancouver Canada – Images courtesy of Naturallywood.com
A NOTE OF CAUTION: critical analysis of new materials
“There’s a lot of things we do because they are good selling points. And we need to be careful of greenwashing… We have a much larger problem with lacking critical thinking when it comes to material selection.” NK
The need for our materials of construction to have a lower or negative embodied carbon is real and pressing. However, care must be taken that climate urgency doesn’t obscure other characteristics of a material. Adoption of low or negative embodied carbon materials must be done in careful consideration of their full lifecycle effect at scale. Considerations include:
- Materials may be toxic to their local environment
- Bio materials that crowd out agricultural crops are not sustainable
- Biochar is a waste product – but carbon sequestration schemes have created a business in growing crops solely to make biochar to bury it
- Natural materials are not necessarily simple: mycelium, for example, can easily produce mould unless managed carefully when growing. Mould spores are a health hazard.
There is also a PR rush to designate materials as low or negative embodied carbon as this is currently fashionable: the term ‘carbon washing’ has been suggested to identify this particular form of greenwashing. In recognition of this and in a step towards regulating the the embodied carbon market, the EU is planning a certification scheme for negative carbon emissions, to be tabled in 2022.
Project Name is a project of IAAC, Institute for Advanced Architecture of Catalonia developed at Masters in Advanced Robotics in 2021 by:
Students: Alfred Bowles, Grace Boyle, Yeo Jeong Kim
Faculty: Mathilde Marengo