In this short research, I tried to get a deeper understanding of how Life Cycle Assessments (LCA) work and what are the challenges of the building material industry and the possible solutions they might have.
Firstly I wanted to understand the LCA process, how comprehensive it is and how easy it is to hide certain material production flaws.
The first important thing to know is that manufacturing companies are the ones that program the LCAs. They set the parameters in which their product will be assessed. They do this to comply with regulations, which means their LCA will be reviewed by third parties; to satisfy customer demand, environmental aspects are becoming more important in consumer habits; and to lead by example, improving the brand image.
An LCA has 4 phases [1]:
The first one defines the goal and scope of the LCA. As a start, we need to define the functional unit that will be analysed – Kg, Tonnes, m2, m3…- and the impact categories that are going to be measured – climate change potential, ozone depletion, acidification… Seeing this from a purely corporate point of view, a product could be evaluated by choosing a more forgiving base unit – using a mass unit instead of a volume one for high-density materials, for example [2]- and not assessing certain impact categories which would end up not showing the full picture.
“The functional unit selected 1Kg of material. This can be useful to initiate accounting of the building LCA but it is useless to compare the relative merit of two materials if these materials have different physical properties. […] For instance, the embodied energy of columns made of concrete, steel and compressed soil block are similar in magnitude for an equal net supported load” [2].
In this phase, it is also defined which parts of the product life cycle will be considered. These are the extraction of raw materials, processing, transportation, use phase and waste phase. And depending on how many are evaluated we find labels like “cradle to cradle” (it considers the five parts), “cradle to grave” (it considers until the end of the use phase), “cradle to gate” (it considers only until transportation)…
Defining what to study and how to do so also means defining what to leave out. Making a complete LCA is extremely complicated, almost impossible, so it is important to know when to stop.
As LCAs are tailored to the manufacturer’s needs, comparison between different LCAs is extremely complicated. To solve this problem, Environmental Product Declarations (EPD) are meant to provide quantified environmental information about the life cycle of a product to facilitate comparison between those that perform the same function.EPDs are operated by Product Category Rules (PCR) which set out the guidelines to develop LCA studies. The problem lies in the fact that PCRs might be set by anyone who calls themselves a programme operator, causing great variation between these rules [3].
The second phase is the Inventory Analysis. This means looking at environmental inputs and outputs of what is measured and gathering data for the analysis. We need to set the regulations/criteria we want to fulfil and collect the data to see if they are fulfilled.
This is the most time-consuming process and the more complex and comprehensive we want the LCA to be, the more difficult and prolonged this phase will be. To reduce complexity, there are life-cycle inventory databases that give us an indication of the environmental impact a material has from which we can extrapolate to our particular case. If there is no data available and we lack the means to collect it, relying upon industry averages is the only solution left and the simplicity of this process depends on the transparency of the supply chains.
The third phase is translating the gathered data into our impact category of choice measured in equivalents (-e). Global warming potential, for example, is measured in CO2-e emissions which also include other global warming gases.
Finally, there is a fourth phase of interpreting the data following the ISO14044 norm that defines LCAs. It means conducting a sensitivity assessment to know where the analysis has limitations and how consistently it was done to look for possible improvements. If the assessment has been conducted for official purposes, external verifiers need to validate it.
After this quick overview in LCA, it is easy to identify its flaws. First, the fact that interested parties define the LCA initial parameters – functional unit, impact categories to assess…- gives them the possibility to hide multiple issues. Secondly, understanding the difficulty of comparison between assessments, their subjectivity and the lack of standardization reduces the LCA’s chances of becoming a useful and credible tool. Thirdly, doing a comprehensive LCA needs a large amount of information that might not be available and trusting industry averages is not a suitable option in all cases.
It is also evident that there are many things affecting product life cycles that are not even remotely considered by an LCA. For example, during the long life of an extraction or processing plant, environmental catastrophes – red sludge flood in Kolontar, Hungary (Fig. 1) – or regular incidents – weekly uncontrolled exhausts in the Rezola cement plant, Spain, not considered in the annual pollution report – might probably happen. Also, the types of pollution assessed in the different impact categories do not take into account other equally important forms of contamination: noise, volatile organic compounds…

Fig. 1: Aerial view of the town of Kolontar covered by toxic red mud. (
https://www.cbc.ca/news/world/)
In conclusion, not only do Life Cycle Assessments have room for improvement as they currently are but also would need to evaluate broader aspects to get meaningful results. Besides, it is unclear whether improvement to a particular product has any global significance. We need to understand materials and material dynamics globally to identify changes that could make a global impact [4].
A material that has the potential for generating global impact but could easily lose it if subjected to foul practices is wood. There is a common thought that building with wood is inherently good as every tree acts like carbon storage. In reality, the amount of stored carbon can be easily matched and surpassed by the high-polluting processes related to its extraction and transportation (Fig. 2).

Fig. 2: Wooden pavilion in Madrid made out of timber brought from the USA. Probably surpassing the amount of stored carbon of the wood during transportation. (
https://elpais.com/ccaa/2020/01/30/madrid/1580405166_018783.html)
Making this worse, due to climate change, some forests, in Canada for example, are no longer carbon sinks but carbon emitters. In essence, this depends on what wins if forest death or growth. Fires, plagues and other natural disturbances, mostly outside the control of humans, though greatly aggravated by them, significantly impact the ability of forests to absorb more CO2 than they emit. Products built from this wood are no longer carbon sinks.
Counting stored carbon in timber as independent from the forest it comes from, it might not be a carbon sink, and the rest of the processes will worsen the issue as demand will grow without understanding the scope. Timber cannot be used as a claim for carbon neutrality based on a poor LCA that masks ill-considered forestry dynamics, it is crucial to understand the role the trees and hence the building play in the forest. As mentioned before, LCAs only consider the extraction process but not the extracted material, which in wood is the time it makes the carbon sequestration [5].
The limited supply of timber also poses a challenge. Biomass is used for many things and available and suitable land for forestry is limited and shrinking because of desertification (Fig. 3). The total biomass appropriation by the building industry cannot rise significantly as we are not far from approaching the limit of supply. Recycling is a great option but there will always be the need for new material inflow.
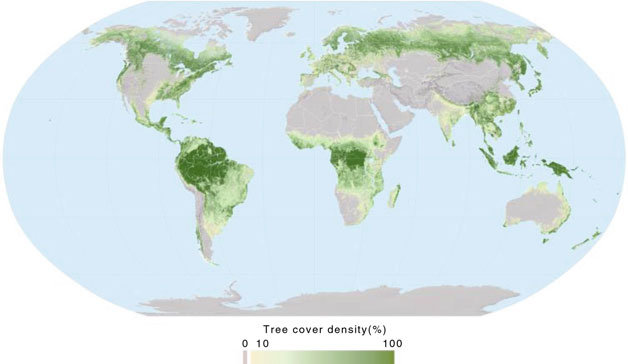
Fig. 3: Global forest cover map (FAO 2010. Forests of the World.
http://data.fao.org)
Even though the previous paragraphs might seem depressing, wood has the potential to make a shift in the building industry but this will not happen just by substituting one material for the other. There is a need to understand not only wood but every material and its supply chain in a holistic way.
“Global demand for engineering materials has quadrupled in the past 50 years. […] based on assumed population growth to over 9 billion (10^9), and economic growth giving per capita wealth three times greater than the present, forecasts that demand for materials will by 2050 be at least double current levels” [4].
“The global construction industry consumes more raw materials (3000 Mt/year, almost 50% by weight) than any other economic activity, which shows a clearly unsustainable industry” [6].
“At world level, civil works and building construction consumes 60% of the raw materials extracted from the lithosphere. From this volume, buildings represent 40%, in other words, 24% of these global extractions” [2].
Some predictions state that with the current demographic trends, the need for construction materials will be double in the coming decades and, as highlighted in different papers, there is great room for improvement in the material efficiency of a few key materials. In particular, extraction and refining processes are the ones with the highest potential to reduce waste production improving material usage.
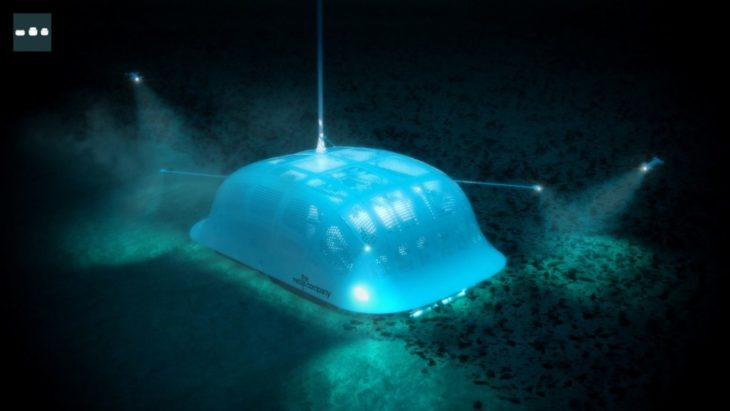
Fig. 4: BIG Deepgreen project sources rare minerals from the ocean bed (
https://www.big.dk)
Most construction materials come from the combination of different mineral products and it is unlikely that we run out of them. However, with the exploitation of current deposits and the increasingly accurate estimates of their extractive capacities comes price rise and the increase in exploration efforts in search of new sources (Fig. 4). Nevertheless, over the past years, these explorations have slowly been giving less meaningful results reducing the chances of finding new major hidden reservoirs. What may happen in the future is that the technological effort to extract scarce quantities of material from remote locations will no longer be economically suitable.
Processing and refining is the most energy-intensive part of material production. There are four fields to tackle in which energy-saving and waste reduction could have a great impact.
First, working towards energy efficiency in just a handful of materials (Fig. 5). Trying to move towards best practices in the most mainstream materials could save up to 40% of carbon emissions. Operational improvement and supply chain redesign could give further gains. The biggest problem lies in the optimised processes that have been streamlined for the most used materials in which their supply chains have almost reached their thermodynamic limit [4].

Fig. 5: Breakdown of global CO2 emissions in 2006 demonstrating the importance of five key materials [4]
Thirdly, increasing the rate of reusing and recycling would reduce the amount of material needed for extraction. The challenges these techniques currently pose are threefold. There is a technical one in which repeatedly recycling increases material impurities hinder the physical capabilities of the product or increase the amount of recycled material needed for a unit of manufactured product. Besides, mixed materials generate mixed waste difficult to separate. There is an economic one as collection and separation are costly. And lastly, there is an operational one in as there is uncertainty in the availability of recycled materials. Reusing and recycling will never meet demand as they cannot supply materials for new construction and replacements but they could reduce the exploitation rates of known reserves. Another aspect to take into consideration is that tailored building elements may not be easily recycled and the savings in the material you make during the manufacturing process may reduce the element’s lifespan.
Lastly, switching to green energy alternatives will greatly impact the carbon production of material processing while still allowing energy-intensive and not extremely optimised processes to happen.
The aforementioned fields on their own have limited power to change the current situation as applying the best available practices would not reduce emissions by over 50% [4].
Material efficiency is still an underdeveloped topic but its impact in the manufacturing industry could be huge. The main barriers that exist, as always, have to do with money. The high investments that have been done in machinery were made in a time when energy and material were cheaper. The final price never reflects the environmental impact of the material and its manufacturing. There will always be demand for new products so it is not financially attractive to improve foul processes.
We draw many conclusions from this research:
-It is obvious that LCAs are incomplete and need to be standardised. They cannot be used as the single measure of a product’s environmental friendliness.
-New policies need to economically punish ill practices. They also need to be set after understanding the field and based on current best technologies and reasonable estimates, not setting easily achievable standards.
-Designers play a key role and need to make an effort in understanding the local supply chains and environment in our designs and see how the use of different materials can improve them.
-There is a great development to be made in the supply chains in multiple areas which reduce the complexity of tackling one overwhelmingly complex problem.
-As consumers, we need to understand materials as extremely valuable despite their low price. The way we consume and the products we buy could slowly model the manufacturing industry.
-Instead of looking for improvement in current technologies, there is a need to search for future plausible scenarios challenging and achievable enough to move the industry in the right direction.
References:
[1] www.ecochain.com/knowledge/life-cycle-assessment-lca-guide/
[2] Ignacio Z. Antonio V. Alfonso A. Life cycle assessment of building materials: Comparative analysis of energy and environmental impacts and evaluation of the eco-efficiency improvement. www.researchgate.net/. Building and Environment 46 1133-1140 (2010)
[3] Alina V., Olga A, Boris B. Life Cycle Assessment (LCA) in building materials industry. MATEC Web of Conferences 106, 08059 (2017).
[4] Julian M. A., Michael F. A, Timothy G. G, Ernst W. Material efficiency: A white paper. www.researchgate.net/. Resources, Conservation and Recycling 55 362-381 (2010).
[5] Kiel M. Op-ed: There’s more to timber building than trees. www.archpaper.com/2021/03/op-ed-more-to-timber-building-than-trees/. (2021)
[6] F. Pacheco-Torgal, J.A. Labrincha. The future of construction materials research and the seventh UN Millennium Development Goal: A few insights. www.researchgate.net/. Construction and Building Materials 40 729-737 (2012).
“Are LCAs enough?: Brief introduction to eco-efficiency and material dynamics and possible areas for improvement” is a short research of IAAC, Intitute for Advanced Architecture of Catalonia developed at the Masters in Advanced Computation for Architecture and Design in 2021 by:
Student: Pablo Antuña Molina